N. Einstein BSME1,3, Julie Faieta MOT, OTR/L2,3, Jack Reifenberg2,3, C. DiGiovine, PhD ATP/SMS1,2,3,4, S. Metzler, DSc1,2,3,4
1College of Engineering, 2School of Health and Rehabilitation Sciences, 3Rehabilitation Science and Technology Lab, The Ohio State University; 4Assistive Technology Center, The Ohio State University Wexner Medical Center
INTRODUCTION
Manual wheelchair users utilize their upper body extensively to generate the necessary forces for propulsion, and as a result, they are susceptible to musculoskeletal upper extremity injuries.[1] These biomechanically based injuries are often related to propulsion techniques and individual wheelchair configuration.[2,3] In order to better understand how propulsion metrics such as stroke frequency, stroke length and push force relate to biomechanical injury, it is necessary to collect data that can be used to evaluate these metrics over an extended period of time. Currently, a device known as the SmartWheel, manufactured by Out-Front, can be used in a clinical setting to generate a report summarizing these metrics. [4,5] However, this device has a number of limitations that prevent its use in either long-term studies, or to observe patterns of everyday use outside the clinic. The SmartWheel incorporates a range of different sensors in a standalone wheel that is substituted for standard, original equipment wheelchair wheels when in use. The SmartWheel is also relatively expensive, at a retail cost of $6000.00. In practice, the SmartWheel is limited to use in the clinic because of its cost, its weight relative to a typical spoked wheel, and the need to reconfigure the consumer’s wheelchair.
With the objective of overcoming these limitations and designing a reasonably priced device for more widespread use, we have developed a novel device, called the SmartHub. The SmartHub is a low cost (approx. $100.00 for hardware), unobtrusive activity monitor designed to collect, and either store or transmit wheelchair propulsion data. This device is approximately the size of a hockey puck, and consists of a WIFI- enabled microprocessor, nine-axis inertial measurement unit, and rechargeable battery that can be easily attached to any existing, original equipment manual wheelchair wheel. The SmartHub collects a wide range of propulsion characteristics in real-time, which can be utilized to produce the metrics of interest. The SmartHub and the resulting information it produces have the potential to allow the study and evaluation of these metrics over a much greater range of use on a user’s existing wheelchair configuration, with the goal of reducing upper extremity injuries for manual wheelchair users.
METHODS
Initial Iteration
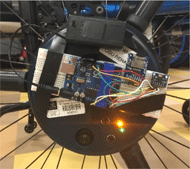
Once data is taken and stored locally on the SD card, it is manually transferred to a computer, in which a uniquely developed MATLAB script reads the raw data and outputs propulsion metrics in a visual manner, making it readable for both wheelchair users and clinicians.
However, this design iteration has several limitations. Firstly, the device has no proper fixation method to the wheelchair, currently only tape is used, causing inconsistent placement resulting in inaccurate data collection. Additionally, by using a microcontroller, only one program can be run on the device, limiting flexibility and versatility. Once data is collected, it must be inelegantly transferred manually. Future designs would increase data accuracy, while introducing wireless capability, all encased within a portable, adaptable, and robust housing.
Current Design
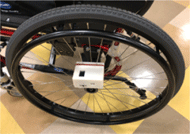
The brain of the SmartHub is a Linux-based microprocessor, Raspberry Pi Zero W. At a cost of $5.00, and equipped with friendly general-purpose input output, this small form-factor board allows the SmartHub to store and execute a multitude of programs simultaneously will providing various means of communication to host devices. Included on this board is a micro-SD card reader, which is used as a boot drive and removable storage. Additionally, an OLED screen is used to display informative runtime feedback for both clinicians and wheelchair users.
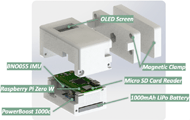
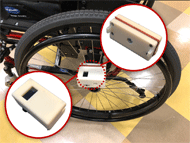
Software
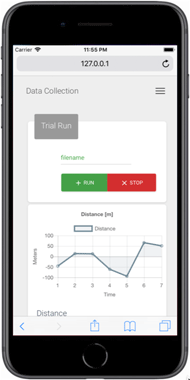
microcontroller that is limited to execute one program exclusively, a Raspberry Pi Zero W microprocessor was used, which increases both flexibility and processing power. The Linux-based board also includes Bluetooth and WIFI for wireless connectivity, all within a footprint half the size of the Arduino used initially.
The SmartHub is programmed to include both wired and wireless connectivity upon bootup. When plugged in via micro-USB 2.0, the SmartHub bridges the host computers internet access and is able to receive updates in addition to communication. Development and the majority of programming was done over this protocol. Additionally, upon bootup, the SmartHub creates and broadcasts its own 802.11b WIFI network. In order to connect to the device, a host computer simply needs to connect to the ’SmartHub’ wireless network and enter in proper credentials. This peer to peer (P2P) method is robust and encrypted for seamless and secure data transfer.
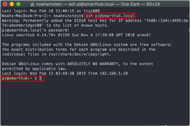
(iOS, Android, OSX, Windows) can connect and interact with the SmartHub. For versatility and ubiquity, Python was used for all SmartHub code. Programs for data collection, HTML webpage hosting, and post-processing were all built from the ground up and by using a standard language, code fluidity is maximized for future development.
Because the entirety of the source code, including the OS image, is comprehensive, a robust version control infrastructure was created to ensure optimal code tracking and user modification of all code. Additionally, this version control system allows for roll-back ability in the case of broken or damaged code and the ability to assign simultaneous working tasks for future developers. All SmartHub code is hosted on a private repository on GitHub.
OUTCOMES
Data Validation
Clinical application of the SmartWheel in testing and evaluation was primarily focused on a singular propulsion test: a ten-meter distance test in which stroke data and push force are calculated in a manner that relies on knowledge of the type of surface material (carpet, tile, wood, etc.). In order to validate the SmartHub and its output, we utilized a specific wheelchair configuration- a manual wheelchair (Invacare TRA) with one rear wheel configured as a SmartWheel and the other rear wheel configured as a standard wheelchair wheel with the SmartHub attached. We conducted two validation tests: 1) ten meters on tile; 2) ten meters on carpet. Because the SmartHub can calculate directional heading, in addition to validation testing with the SmartWheel, the SmartHub was also tested in the standard Wheelchair Skills Program (WSP) [6], which involves a sequence of specific activities that are used to evaluate wheelchair users’ effectiveness and abilities. These activities include maneuvering on inclined ramps, figure-8 movements on a flat surface, and oval track distance tests. To test validity of heading, subjects conducted the figure-8 protocol of the WSP.
Results
Metric
|
Percent Error [%]
|
|
---|---|---|
Tile
|
Carpet
|
|
Distance
|
3.41
|
3.32
|
Stroke Length
|
7.05
|
9.09
|
Average Stroke Velocity
|
8.22
|
8.50
|
Average Stroke Frequency
|
4.91
|
5.47
|
Peak Tangential Force
|
16.74
|
22.98
|
The percent error for each metric is calculated as the average of all absolute values of the difference in the SmartWheel data point and SmartHub data point divided by the SmartWheel data point. Average percent error of the SmartHub data as compared to the SmartWheel for all validation trials was then calculated over all stroke locations and represented in Table 2.
The validation data show that the SmartHub is more accurate on the tile surface than the carpeted surface, however, the relative error with respect to individual metrics appears consistent regardless of surface type and is sufficient for clinicians.
The data for distance, heading, and path of travel for a figure-8 test are shown in Figure 7. Included in this figure are three plots- increasing distance over time, wheelchair heading over time, and the resulting vectorized trajectory of the wheelchair from a birds-eye perspective.
Discussion
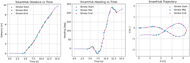
COST
Part Name
|
Description
|
Quantity
|
Cost
|
Subtotal
|
---|---|---|---|---|
Raspberry Pi Zero W
|
Microprocessor
|
1
|
$ 5.00
|
$ 5.00
|
IMU
|
BNO055 9-axis gyroscope, accelerometer, magnetometer
|
1
|
$ 38.18
|
$ 38.18
|
PowerBooster
|
Powers SmartHub and recharges internal battery
|
1
|
$ 20.99
|
$ 20.99
|
Screen
|
Provides helpful feedback quickly
|
1
|
$ 9.99
|
$ 9.99
|
Micro SD Card
|
Boot drive and storage device
|
1
|
$ 7.99
|
$ 7.99
|
Rechargeable Battery
|
1000mAh SmartHub power source
|
1
|
$ 8.99
|
$ 8.99
|
Mounting Equipment
|
Screws, magnets, bolt and nut
|
1
|
$ 2.64
|
$ 3.63
|
ABS Filament
|
3D Printed Housing
|
1
|
$ 15.00
|
$ 15.00
|
TOTAL
|
$110.05
|
IMPLICATIONS
While the SmartWheel is currently suited only to use in a clinical setting, the SmartHub has the potential for use in any range of settings, inside and outside the clinic due to its portability, hardware adaptability and increased functionality for the wheelchair user. As such, it can be used to provide clinicians and users with a broad understanding of propulsion techniques. Manual wheelchair users could benefit from accurate propulsion metrics gathered in a simple, unobtrusive manner. The SmartHub is one example of a tool that can be utilized for insights to optimize healthcare delivery and outcomes. Specifically, the SmartHub has the potential to help people who utilize manual wheelchairs by identifying ways to reduce injuries and optimizing their mobility.
REFERENCES
[1] Curtis, K. A., Drysdale, G. A., Lanza, R. D., Kolber, M., Vitolo, R. S., & West, R. (1999). Shoulder pain in wheelchair users with tetraplegia and paraplegia. Archives of physical medicine and rehabilitation, 80(4), 453-457.
[2] Ferrero, G., Mijno, E., Actis, M. V., Zampa, A., Ratto, N., Arpaia, A., & Massè, A. (2015). Risk factors for shoulder pain in patients with spinal cord injury: a multicenter study. Musculoskeletal surgery, 99(1), 53-56.
[3] Bickelhaupt, B., Oyama, S., Benfield, J., Burau, K., Lee, S., & Trbovich, M. (2018). Effect of Wheelchair Stroke Pattern on Upper Extremity Muscle Fatigue. PM&R.
[4] "SmartWheel," Out-Front, 2015. [Online]. Available: http://www.out- front.com/smartwheel_overview.php.
[5] Cooper R. A., "SmartWheel: From concept to clinical practice," Prosthetics and Orthotics International, vol. 33, no. 3, pp. 198-209, 2009.
[6] Wheelchair Skills Program Manual. http://www.wheelchairskillsprogram.ca/eng/manual. Accessed December 30, 2015.