Brett English, Charles Martin, Sreeram Nagappa, Nickolaus Will, Shanmugam Muruga Palaniappan, Shruthi Suresh, Ting Zhang
1. Problem Statement/Research: Question and Background
Paralysis or weakness of the muscles in the wrist makes it difficult for individuals with high-level spinal cord injuries (SCI), carpal tunnel or stroke to perform daily manual activities such as eating, writing, unlocking doors with keys or swiping credit cards [1][2] . Without appropriate treatment opportunities, there exists the risk of developing a clenched fist from contractures, which may exacerbate problems performing typical activities of daily living (ADL) and hygiene maintenance[3]
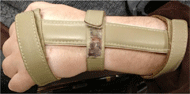
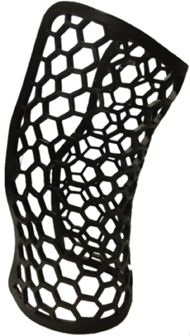
In today’s smart-age, the traditional wrist orthotic needs a makeover. We designed the WristSense (Figure 2), a rapidly prototyped wrist brace outfitted with off-the-shelf electronics and the power of artificial intelligence. In addition to providing the required amount of support, the WristSense also allows users to use gestures to control customizable outputs. The use of AI allows users to train customizable gestures that are most intuitive to them to perform.
2. Methods/Approach/Solutions Considered
The WristSense has been developed through an iterative design process wherein the team first identified the needs of the user, and then designed several versions of the wrist orthotic which meet these needs best. The primary user defined that they would need a light- weight, multi-functional wrist orthotic which could be activated with gesture control. We decided that the use of rapid prototyping techniques, such as 3D printing, would be ideal for the design of WristSense. This would enable individuals with access to 3D printers to print their own wrist orthotics based on the designs the team has developed. Furthermore, off-the- shelf electronics and sensors were used in all iterations of the WristSense to allow gesture recognition. We designed and implemented a unique machine learning algorithm to learn different gestures trained by users and implemented it in the WristSense[11].
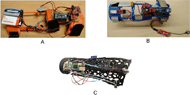
In the second iteration, in addition to 3D printing a more streamlined version of the traditional wrist orthotic, the team also identified different mounting techniques for the electronics to make it less encumbered. As can be seen in Figure 3A and 3B, a smaller battery pack was used, and the number of electronics chosen were significantly reduced. In the original design of the WristSense, the Arduino was the microprocessor chosen to handle the communication between the sensors and the various tools.
Through the different prototypes, we determined that a more moldable version of the 3D printed plastic was a suitable solution to allow customizability of the wrist orthotic for different individuals. In the third prototype, the team explored 3D scanning as an alternative technique to allow a better fit of the WristSense (Figure 3C). In this iteration, we also decided to use a Raspberry Pi as the computational element to serve as an interface between the sensors and the output tools. However, 3D scanning required the use of special equipment( 3D scanner), which is not as widely available as a 3D printer. Moreover, 3D scans of the arm were not consistent and printing a customized model took upwards of 20 hours.
3. Description of Final Approach and Design
The final design of the WristSense comprises of two parts, a 3D printed plastic body and off-the-shelf electronics to facilitate gesture recognition and customizability of the tools used. For the development of the WristSense, the team prioritized developing a solution which was a) easily and rapidly manufactured/fabricated, b) customizable fit, and c) customizable control.
A. Easilyandrapidlymanufactured/fabricated.
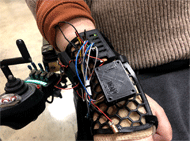
The electronics used for the control of the WristSense are inexpensive, off-the-shelf components. They include a Raspberry Pi, an inertial measurement unit (IMU) which combines the functionality of an accelerometer and gyroscope, and a rechargeable battery pack. These components can be easily assembled, and the Raspberry Pi runs a python service which, when turned on, allows the recognition of gestures.
B. Customizablefit
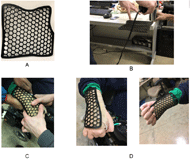
C. Customizable control
There are two aspects of customizable control: gesture recognition and the
controllable tools. For the gesture recognition, we implemented a dynamic time warping based machine learning algorithm. This algorithm uses data from the IMU to allow users to train the system with gestures they find most comfortable or intuitive for them. The users first determine the gestures they want to perform based on the ones that are most convenient for them. They then run the training algorithm which requests them to repeat each gesture being trained four times. Once the system has been trained, it saves the gesture profile of the user. This can be reset if the user finds other gestures which are more comfortable.
The activation of the WristSense is critical in order to prevent unintentional activation. The options for activation methods can be customized based on individual preferences and abilities and may include electromyography (EMG), gestures, or touch switches. In our final design, the WristSense is activated with the press of a push button. Once the WristSense is activated, the ‘listening’ mode is active during which it identifies the gesture being performed by the user.
The users can also link gestures to different outputs. For instance, the user can turn on a coffee maker with a specific gesture, while another gesture controls the lights. The WristSense can communicate with any smart-device using Bluetooth or WiFi capabilities. This allows gestures to control any internet-of-things enabled device. In the presented iteration of the WristSense, our user wanted to control a laser pointer and a buzzer using gestures that were convenient for him.
4. Outcome (Results of any outcomes testing and/or user feedback)
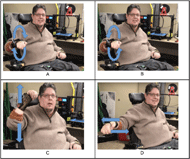
The WristSense had an almost 100% accuracy in detecting the four gestures and activating the linked outputs- in this case, a laser pointer and a buzzer (refer to video). The user reported that the WristSense was comfortable to wear in the short-term. Future work will involve extensive testing of the comfort of the WristSense for long-term wear.
5. Cost (Cost to produce and expected pricing)
The table below lists the cost price of making the WristSense. We estimate that it would cost $91.50 to make one WristSense. The WristSense will be sold at $200. Since the WristSense will be covered by insurance, we expect that it will be easily adopted by the community. Moreover, with the customizable ability of the WristSense we eventually anticipate being able to open-source the CAD file for the WristSense allowing other individuals to 3D print their own and providing them with the kit to make it a smart-device. This would involve a completely different business model.
Materials
|
Cost (USD)
|
---|---|
3D printing filament (100g)
|
5.00
|
Raspberry Pi
|
24.50
|
IMU
|
28.50
|
Electronics (battery, button, laser, buzzer)
|
20.00
|
Fabric wrist brace
|
13.50
|
Total Cost
|
91.5
|
6. Significance
The WristSense is designed to be a universal tool for people who use wrist orthoses to perform activities of daily life. The ability of the wearer to program gestures they find most comfortable allows a high degree of customizability. Moreover, the 3D printed nature and the ease of availability of the electronics would allow easy deployment or creation of the lightweight wrist orthotic. The WristSense can also be used to activate or deploy various lightweight tools attached to the orthotic, like an automated “Swiss Army” knife. Ultimately, the WristSense would be able to control various smart-devices such as a smart thermostat, a coffee machine or even a smart-home.
This would improve the usability of the traditional wrist brace and allow users to adopt the WristSense more easily. The modular nature of the device allows various attachments to be added and motorized to allow more independence. In this particular case, our user, a professor, enjoyed the use of the WristSense as a laser pointer with which he could explain his slides. The WristSense would open more employment opportunities for people with upper limb impairments, increase their independence and productivity, as well as reduce their reliance on caregiver services.
We also anticipate that the technology can be used by people who are able-bodied as well. It would enable them to perform any gesture to control their smart-devices.
References
- C. K. Thomas, E. Y. Zaidner, B. Calancie, J. G. Broton, and B. R. Bigland-Ritchie, “Muscle weakness, paralysis, and atrophy after human cervical spinal cord injury,” Exp Neurol, vol. 148, no. 0014–4886 (Print), pp. 414–423, 1997.
- A. Andringa, I. van de Port, and J.-W. Meijer, “Long-term use of a static hand-wrist orthosis in chronic stroke patients: a pilot study.,” Stroke Res. Treat., vol. 2013, p. 546093, 2013.
- I. C. M. Heijnen, R. J. P. Franken, B. J. W. Bevaart, and J. W. G. Meijer, “Long-term outcome of superficialis-to-profundus tendon transfer in patients with clenched fist due to spastic hemiplegia,” Disabil. Rehabil., vol. 30, no. 9, pp. 675–678, Jan. 2008.
- K. Nas, L. Yazmalar, V. Şah, A. Aydın, and K. Öneş, “Rehabilitation of spinal cord injuries.,” World J. Orthop., vol. 6, no. 1, pp. 8–16, Jan. 2015.
- A. A. Freehafer, “Care of the hand in cervical spinal cord injuries,” Spinal Cord, vol. 7, no. 2, pp. 118–130, Aug. 1969.
- Y. S. Kang, Y. G. Park, B. S. Lee, and H. S. Park, “Biomechanical evaluation of wrist- driven flexor hinge orthosis in persons with spinal cord injury,” J Rehabil Res Dev, vol. 50, no. 8, pp. 1129–1138, 2013.
- Z. O. Khokhar, Z. G. Xiao, and C. Menon, “Surface EMG pattern recognition for real- time control of a wrist exoskeleton.,” Biomed. Eng. Online, vol. 9, p. 41, 2010.
- E. Mainardi and A. Davalli, “Controlling a prosthetic arm with a throat microphone.,” Conf. Proc. ... Annu. Int. Conf. IEEE Eng. Med. Biol. Soc. IEEE Eng. Med. Biol. Soc. Annu. Conf., vol. 2007, pp. 3035–9, Jan. 2007.
- [D. P. Romilly, C. Anglin, R. G. Gosine, C. Hershler, and S. U. Raschke, “A Functional Task Analysis and Motion Simulation for the Development of a Powered Upper-Limb Orthosis,” IEEE Trans. Rehabil. Eng., vol. 2, no. 3, pp. 119–129, 1994.
- BCC Research, “Bionics: Technologies and Global Markets,” 2017.
- S. Suresh, S. Manda, C. Marrero, L. Jacob, and B. S. Duerstock, “Multi-functional Wrist Orthotic with Universal Gesture Recognition System,” in RESNA 2017 Annual Conference, 2017.
Acknowledgements and References
We want to acknowledge and thank Gabriel Ng for his efforts in helping with the voiceover for our video.