Kelvin H.L. Heung, Zhiqiang Tang, Leo Ho, Macro Tung
Department of Biomedical Engineering, The Chinese University of Hong KongProblem Statement/Research Question and Background
Stroke has been well-known as the most common cause of disability and death worldwide. Every year there are estimated to be 15 million of people who have experienced a stroke [1]. Loss of hand mobility is observed on most stroke patients, which inhibits their activities of daily living (ADL) and reduces patients’ quality of life (QOL) [2]. Rehabilitation exercises including active, repetitive, task-specific upper-limb movement are suggested for improving the function of impaired hand within the first six months after a stroke [3], but not all the patients can receive such treatment due to insufficient number of well-trained physiotherapists [4]. Therefore, researchers introduced robotic hand devices for helping provide more intensive rehabilitation training to patients. Traditional actuation mechanisms of hand rehabilitation devices can be classified into linkage-based [5] and wire-driven [6]. Although their clinical efficacy has been proven [7], [8], drawback exists in the reduced level of comfort and compliance due to the bulkiness and constant stretching of fingers [9]. As a result, these devices hinder the performance of daily activities assistance.
Soft robotic hands/gloves that are pneumatically actuated are proposed to improve the compliance of traditional devices [10], [11]. Utilizing soft materials, e.g. silicone rubber, fabric, etc. can allow the soft robotic devices to be compact due to the low inherent stiffness and high compliance of soft materials [12]. Examples of existing soft robotic hands include the soft robotic glove by Polygerinos et al. [10], and the ‘EsoGlove’ by Yap et al. [11]. However, in hand rehabilitation, finger flexion and extension are of equal importance. The soft robotic glove passively controls finger extension by the very finite elasticity of elastomeric actuators on fluid depressurization. The insufficient extension force created by the limited elasticity of elastomer would not be able to facilitate hand opening for stroke survivors suffering from significant levels of poststroke finger spasticity due to increased muscle tone in finger flexors [13], [14]. Another bi-directional soft robotic glove is further proposed to increase the extension torque [14]. The glove generally controls finger extension by placing a thermoplastic polyurethane (TPU)-based airbag-like extension actuator underneath to the bending actuator, allowing the actuator to be straightened up on the inflation of bottom extension actuator. Still, the overall size of each bi-directional actuator become bulky for reducing the bending resistance imposed by the bottom extension actuator, making the glove to be hard to fit to stroke survivors.
Methods/Approach/Solutions Considered
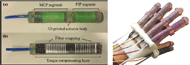
Compared with conventional robotic devices, our 3D-print soft robotic hand therefore can assist patients in performing more hand function tasks for aiding in activities of daily living (ADL), for example, wringing a towel and gripping a pen. These kinds of daily tasks are difficult to be completed when patients are using the conventional metallic robotic devices because of their bulkiness. The system is controlled by user intention (e.g. muscle activities [EMG] and brainwave[EEG]) to facilitate neuro-rehabilitation to regain hand function after stroke.
Description of Final Approach and Design
The SECA presented includes an 3D printed elastomer bladder reinforced with fiber wrapping and a torque compensating layer (see Figure 1). The composite design with a torque compensating layer can facilitate both flexion and extension on the same unit. On pressurization, the fiber wrapping eliminates radial expansion and the torque compensating layer further restricts bottom axial elongation, resulting in bending motion. On depressurization, the torque compensating layer facilitates the SECA to extend to its initial undeformed position. Meanwhile, the aforementioned soft robotic hand designs allow flexion only without considering extension.
Multiple SECAs are then integrated to a 3D printed hand base as a mean of securing the actuators to finger joints (see Figure 1). The 3D printed hand base is designed to fit with the dorsal surface of the palm, enabling a better hand fitting design. Open-palm design adopted also allows the soft robotic hand to be easily put on stroke survivors with tightly clenched hand. Air tubes are connected to all the SECAs for supplying input fluid pressure to actuate finger flexion and extension. Total weight of the 3D printed soft robotic hand is approximately 200 grams, which will not create extra burden to the impaired hand that may impede natural hand movement.
Outcome (Results of any outcomes testing and/or user feedback)
Subject A |
Subject B | |
---|---|---|
Age (years) | 71 | 64 |
Gender |
Female | Male |
Hemiplegic side | Left | Right |
Stroke type | Ischemic | Ischemic |
Time after onset |
30 months |
8 months |
Two stroke subjects were recruited to evaluate the effect of rehabilitation training with the new personalized 3D printed soft robotic hand (see Table 1). 20 sessions (3 sessions per week) of hand function rehabilitation training (First 10 sessions: hand opening and closing, remaining 10 sessions: to conduct some activities of daily living (ADL) using the 3D printed soft robotic hand, including to grip an empty plastic bottle (radius: 2.8cm, height: 21.5cm) and to grasp a marker pen (radius: 0.75cm, length: 11.5cm).) were given to each subject. Each session lasted for 45 minutes, while 5 minutes break time was given in each session to prevent muscle fatigue.
As the outcome measurements, the wrist and hand scale of the Fugl-Meyer Assessment for upper extremity (FMA-UE), Box-and-Block test (BBT), and normal grip force (Jamar® Dynamometers, JLW Instruments, U.S.A) assessed before and after 20 sessions of training are compared (see Table 2). FMA-UE evaluates voluntary motor function of upper limb based on the completion of standard movement sets [18]. Box-and-Block test measures unilateral gross manual dexterity by counting the number of moved blocks from one compartment of a box to another of the same size in 1 minute. More moved blocks indicate better hand function [19].
Subject A | Subject B |
|||||
---|---|---|---|---|---|---|
Pre. | Post. |
Diff. | Pre. | Post. |
Diff. | |
Wrist and Hand of FMA-UE (Full: 24) | 10 | 15 | +5 | 12 | 15 | +3 |
BBT | 13 | 15 | +2 | 23 | 37 | +14 |
Grip force (kg) | 6.7 | 7.8 | +1.1 |
10.4 | 11.5 | +1.1 |
From the results, it is observed that both subjects have improvement of their hand function after the rehabilitation training. The increase of grip strength for both subjects is very similar to each other. For subject B, more improvement is observed in the Box-and-Block test, which a significant increase of the moved blocks in 1minute is recorded after the training. In terms of Fugl-Meyer Assessment, similar change is captured on their wrist and hand motor function.
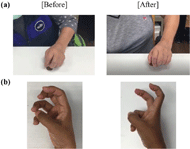
Cost (Cost to produce and expected pricing)
Production Cost |
Expected Pricing |
Printing cost of one SECA: USD $ 200 Total production cost of one soft robotic hand: ~ USD $1,150 |
Total price of one soft robotic hand: ~ USD $2,000 |
Significance
With the emerging market of 3D printing with silicone, even the pediatric stroke patients can have the chance to improve their hand function by participating in the new rehabilitation training program with our 3D printed soft robotic hand. For conventional robotic devices, it was never possible to design a rigid exoskeleton robotic hand to suit all fingers in each individual given the limited choice of electric motors. With all the advancements, our soft robotic hand can be 3D printed to suit any stroke individual with any hand condition, including the small size of hands.
Besides, a new task-oriented rehabilitation training program with our 3D-print soft robotic hand can be potentially introduced to day-care rehabilitation centers and at home. During the rehabilitation training, the patients are asked to perform specific daily tasks, for example, to grasp a glass and to wring a towel. Compared with the traditional training procedure (only requires patients to perform hand closing and opening with the traditional robotic devices), a task-oriented training program will facilitate a better hand function recovery. Therefore, more disabled individuals, including pediatric stroke patients, who are discharged from hospitals can
participate in the rehabilitation training program. The staff members in the centers can also provide hand function training with the assistant of the soft robotic hand. More stroke patients and elderly can have the chance to use the soft robotic device and get recovered.
Last but not least, patients could choose to purchase the 3D-print soft robotic hand and conduct their own training program at home, and therefore the recovery process can be accelerated. Given the aforementioned advantages of our 3D-print soft robotic hand, patients, including pediatric stroke patients, can also use the soft robotic hand anytime at home for ADL assistance as soon as they want extra help during performing the daily tasks. It motivates their willingness in using their impaired hands again, which is important for keeping them participate in stroke rehabilitation training.
References
[1] A. E. Hines, P. E. Crago, and C. Billian, “Hand opening by electrical stimulation in patients with spastic hemiplegia,” IEEE Trans. Rehabil. Eng. 1995; 3(2): 193–205.
[2] C. Takahashi, L. Der-Yeghiaian, V. Le, R. Motiwala, et al., “Robot-based hand motor therapy after stroke,” Brain 2008; 131: 425-437.
[3] K. Lee, S. Lim, K. Kim, et al., “Six-month functional recovery of stroke patients: a multi- time-point study,” Int J Rehabil Res 2015;38: 173–180.
[4] P. A. Healthwear, “Medical technology becomes wearable,” Computer 2004; 37: 42–49.
[5] N. Ho, K. Tong, X. Hu, et al., “An EMG-driven exoskeleton hand robotic training device on chronic stroke subjects: task training system for stroke rehabilitation,” IEEE Int Conf Rehabil Robot 2011;2011: 5975340.
[6] L. Dovat, O. Lambercy, R. Gassert, et al., “HandCARE: A cable-actuated rehabilitation system to train hand function after stroke,” IEEE Trans Neural Syst Rehabil Eng 2008;16(6): 582–591.
[7] X.L. Hu, K.Y. Tong, X.J. Wei, W. Rong, E.A. Susanto, S.K. Ho, “The effects of post- stroke upper-limb training with an electromyography (EMG)-driven hand robot,” J Electromyogr Kinesiol. 2013 Oct;23(5):1065-74
[8] B. Kim, H. In, D.Y. Lee, K.J. Cho, ” Development and assessment of a hand assist device: GRIPIT,” J Neuroeng Rehabil. 2017;21;14(1):15
[9] B. Dellon, Y. Matsuoka., “Prosthetics, exoskeletons, and rehabilitation [grand challenges of robotics],” IEEE Robot Autom Mag 2007;14: 30–34.
[10] H. Yap, J. Lim, F. Nasrallah, et al., “Characterization and evaluation of soft elastomeric actuators for hand assistive and rehabilitation applications,” J. Med. Eng. Technol. 2016;40: 199–209, 2016.
[11] P. Polygerinos, Z. Wang, K.C. Galloway, et al., “Soft robotic glove for combined assistance and at-home rehabilitation.” Robot Auton Syst 2015;73: 135–143.
[12] D. Rus and M. Tolley, “Design, fabrication and control of soft robots,” Nature 2015;(521): 467–475.
[13] K. Heung, R. Tong, A. Lau, Z. Li, “Robotic Glove with Soft-Elastic Composite Actuators for assisting activities of daily living,”, Soft Robot (accepted)
[14] H. Yap, P. Khin, T. Koh, et al., “A fully fabric-based bidirectional soft robotic glove for assistance and rehabilitation of hand impaired patients,” IEEE Robot Autom Let 2017;2: 1383– 1390.
Acknowledgements
This research is supported by the CUHK T Stone Robotics Institute (C4930759), the CUHK Knowledge Transfer Project Fund (KPF18HLF12), and the Hong Kong Innovation and Technology Fund (ITF) (ITS/065/18FP). We would like to express my appreciation to professor Raymond TONG and professor Zheng LI for their support in this project.