Jade Clouâtre1,2
, Charles Doyon
1,2
, Jason Bouffard
2,3
, Alexandre Campeau-Lecours
1,2
1
Department of Mechanical Engineering (Université Laval),
2
Centre for Interdisciplinary Research in Rehabilitation and Social Integration (CIRRIS),
3
Department of Kinesiology (Université Laval)
ABSTRACT
People with upper body disabilities may be limited in their activities of daily living. Assistive robotic arms (ARA) can help by facilitating the execution of daily living tasks and increasing user independence. However, one main drawback is that ARAs are expensive and thus not fully accessible, mainly due to actuation costs. The general goal of the SIARA project is to develop a low-cost assistive robotic arm able to lift household objects and reach the ground as well as the user's mouth. This paper focuses on mechanical innovation concepts to decrease the actuator torque requirements in order to use low-cost actuators. This is performed with two main concepts, namely optimizing the robot kinematic architecture and static balancing.
INTRODUCTION
People living with upper body disabilities rely on caregivers to perform activities of daily living. This restriction of autonomy is problematic in the context of aging population and labor shortage [1-2]. One solution is the use of assistive technologies (AT) to help regain a certain degree of autonomy [1]. In regard to ATs, it has been shown that assistive robotic arms (ARA) can help people living with disabilities by facilitating the execution of daily living tasks, and increasing user independence [3-4]. Indeed, such robots may assist people in various tasks such as eating, drinking, moving various objects, turning book pages, opening and closing doors, and turning on and off electrical and electronic systems [1].
Various ARAs have been developed, such as the Manus Arm [5], later known as iARM (Exact Dynamics) , Raptor [6], JACO [7], Robolink [8], Robotic Grabber, The Weston [9] and others [10-11]. ARAs are usually installed on a wheelchair and comprise between four and six degrees of freedom (DoF). Control interfaces such as joysticks and switches allow the user to control the arm in space to accomplish tasks [12]. As with many ATs, the main barrier to the adoption of ARA is the cost [13-14]. Indeed, ARAs such as JACO and iARM retail in the range of 35,000 USD, which is expensive for the target population. Even so, the number of such devices may not be claimed under government and insurance programs. At the other end of the spectrum, there exists small low-cost toy/hobby robots in the range of 200 to 2,000 USD such as TinkerKit Braccio , Clicbot , Lynxmotion (LSS) , Ctrl and Niryo One . These robots, however, do not provide enough range, motion or payload capacity to be used in practice and accomplish daily living tasks. Still there is an important price gap between the two classes of robots (professional rehabilitation robots and toy robots), with no intermediary solution. The main reason is due to actuation. While low-cost servomotors can be used in robotic hobby/toys due to the small payload and range, professional rehabilitation robots require actuators providing high torque values (between 3.6 and 12.0 Nm for JACO [7]) to accomplish daily living tasks, for an effective payload of 1.8 kg at a 0.9 m reach. For the latter, it is necessary to use actuators such as DC motors along with compact gearboxes and controllers, which are more expensive and lead to a costlier overall solution. Still 81% to 90% of objects manipulated daily weight less than 300 g [15-16]. It is therefore expected that an ARA with smaller actuators combined with innovative mechanical design and control algorithms would fulfill most needs of people living with severe upper limb disabilities.
OBJECTIVES
The general objective of this project is to develop a low-cost assistive robotic arm able to lift household objects, and reach the ground and the user's mouth (when installed on a wheelchair) through mechanical and algorithmic innovations. This paper focuses on mechanical innovation concepts that decrease the actuator torque requirements to enable the use of low-cost actuators. This is performed with two main concepts, namely optimizing the robot kinematic architecture and static balancing. The arm is developed through an iterative process, in collaboration with researchers in engineering and rehabilitation as well as occupational therapists and end users, with a user-centered approach based on Design Thinking [17].
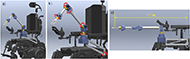
Figure 1.a) SIARA mounted on a wheelchair. b) SIARA's 6 degrees of freedom. c) SIARA's reach.
(Wheelchair 3D model courtesy of Amy Systems)
SUMMARY DESCRIPTION
SIARA (Six-DoF Assistive Robotic Arm) is designed to be mounted on a wheelchair, as shown in Figure 1a. It has 6 DoF (Figure 1b), excluding the opening/closing of the gripper. SIARA has a reach of 1.1 m (Figure 1c) and can hold a payload of 300 g when fully extended, and 600 g when mid-extended; a payload of 300 g covers 81% of 43 of the most important household objects in [15]. When installed on a wheelchair, the robotic arm can reach both the floor and the user's head. It is designed not to interfere with the movements and displacements of the user in his/her environment. The first DoF of SIARA is a statically balanced four-bar mechanism, which reduces the torque required by the first actuator. In this paper, the selection of the architecture is first presented, followed by the presentation of the static balancing, and a first mechanical design.
ARCHITECTURE
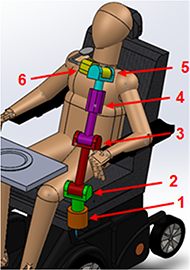
The first step in the design of SIARA was the selection of its architecture. The architecture refers to the number of joints, the type of joints (e.g., rotary, prismatic), their orientation, and their sequence (which one is first and which one follows the other). These choices have an enormous impact on the final solution in terms of required torque values, cumbersomeness, interference with the environment (e.g., wheelchair, user, table), and ease of use. To this end, different architectures have been studied and their advantages/drawbacks are summarized below.
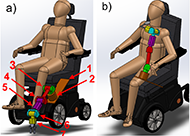
One possible architecture, A-1, shown in Figure 2, is a standard ARA architecture [7]. The spherical wrist of this architecture (axis of joints 4-5-6 intersect at one point) simplifies kinematic calculations. However, the links' length creates high actuator torque requirements for joint 2.
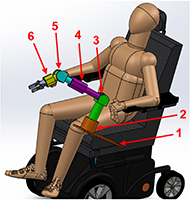
A second architecture, A-2, shown in Figure 3, consists of a 7-DoF solution where a small robotic arm derived from A-1 is mounted on a swivel plate. This way, the length of the arm's links can be reduced, thus requiring high torque values, mainly only for joint 1. However, this architecture has a redundant DoF (joints 1 and 4) which might not be necessary, and which might increase the cost of the solution because of the need for a 7th actuator.
A third architecture, A-3, relies on A-2 with joint 4 removed, as shown in Figure 4. But the robot still reaches both the ground and the user's head. However, the required torque on joint 2 is high when the swivel plate is not parallel to the floor.
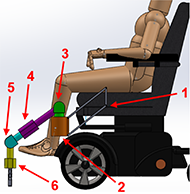
The architecture A-4, based on A-3, replaces the swivel plate by a four-bar mechanism, shown in Figure 5, which reduces the torque provided by the actuator at joint 2. Indeed, thanks to the four-bar mechanism, joint 2 is always parallel to gravity, which reduces considerably the torque required by joint 2.
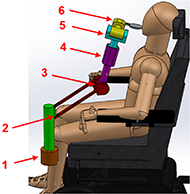
Architecture A-5, shown in Figure 6, is a variant of A-5, but where joints 1 and 2 are reversed. However, in order to reach the user's head, the links would have to be much longer to reach both the floor and the user's mouth, which would increase the torque required by joint 2.
Criteria | Architecture | ||||
---|---|---|---|---|---|
A-1 | A-2 | A-3 | A-4 | A-5 | |
Required torque | |||||
Cumbersomeness | |||||
Number of DoF | 6 | 7 | 6 | 6 | 6 |
In the end, the selected architecture is A-4 (Figure 5) since it best meets the selection criteria presented in Table 2. Indeed, A-4 requires the least amount of torque to the actuators on the arm (joint 2). As for joints 1 and 2, they can be statically balanced to reduce the torque provided by their actuator (presented in the next section).
STATIC BALANCING
Joint | Torque (Nm) | |
---|---|---|
Without balancing | With balancing | |
1 | 7.0 | 1.5 |
3 | 3.5 | 1.0 |
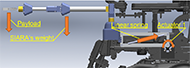
One way to reduce the torque required by the actuators is with static balancing using springs, counterweights or hydraulic cylinders. Since the robot will operate in close proximity to humans, it is important to ensure that it remains safe. If counterweights are positioned too far from the robot, the addition of moving masses can increase the risk of interference with the environment, which is not desirable. If they are too close to the robot, their weight should be high enough so to produce a significant torque for balancing. The preferred method is therefore the installation of springs, which is facilitated by the presence of the four-bar mechanism.
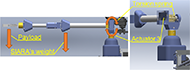
Figure 8. Static balancing of SIARA's joint 3 with a torsion spring.
(Wheelchair 3D model courtesy of Amy Systems)
The balancing of SIARA's joint 1 is shown in Figure 7, where the linear spring force opposes the payload force and the robot's weight, thus reducing the torque provided by the actuator at joint 1. Similarly, Figure 8 shows the static balancing of joint 3, with a torsion spring. Table 2 presents the torque provided by actuators 1 and 3 (the most solicited actuators) with a 300 g payload, without and with static balancing. The springs compensate the robot's weight in its extended position along with 150 g of the payload. Only 150 g of the maximum 300 g payload is balanced because balancing for the full payload would require higher torques from the motors when no payload is present.
MECHANICAL DESIGN
A preliminary design, as shown in Figure 1, was made where the materials were chosen, the actuators selected, and the robot's dimensions defined. The arm will mostly be made of an ABS plastic, while the four-bar mechanism will be made of aluminum, and the actuation will be done by smart servomotors since they are affordable and provide the necessary torque.
DISCUSSION AND CONCLUSION
This paper has presented a 6-DoF assistive robotic arm, SIARA, which aims to help people living with upper body disabilities by facilitating the execution of daily living tasks. The objective was to decrease the actuator torque requirements in order to use low-cost actuators, which in turn would lead to a low-cost overall solution. This was performed by optimizing the robot kinematic architecture along with static balancing. Future work will consist in completing the design and producing a prototype, including actuation and kinematic algorithms. Then, the usability of the prototype will be tested by people living with upper body disabilities with and without experience using an ARA to get their comments and further improve the design.
REFERENCES
- Van der Loos, H. M., Reinkensmeyer, D. J., Guglielmelli, E. (2016). Rehabilitation and healthcare robotics. Springer Handbook of Robotics (pp. 1685-1728). Springer.
- Ministère de la Famille du Québec. Les ainés du Québec, Quelques données récentes, Deuxième ed., 2018.
- Routhier,F., Archambault,P.S., Cyr,M.C., Maheu,V., … & Lemay, M. (2014). Benefits of JACO robotic arm on independent living and social participation. Rehab Eng and Assist Tech Society of North America (RESNA) Conf.
- Beaudoin, M., Lettre, J., Routhier, F., Archambault, P.S., Lemay, M., Gélinas, I. (2019). Long-term use of the JACO robotic arm: a case series, Disability and Rehabilitation: Assistive Technology, 14:3, 267-275
- Driessen, B.J.F., Evers, H.G., Woerden, J.A.v. (2001). Manus – A Wheelchair-Mounted Rehabilitation Robot. Proceedings of the Institution of Mech Eng, Part H: Journal of Eng in Medicine, 215(3):285– 290.
- Mahoney R.M. (2001). The Raptor Wheelchair Robot System. Integration of Assistive Tech in the Inf Age.
- Campeau-Lecours, A., Lamontagne, H., Latour, S., ... & L'Ecuyer, L.J.C. (2019). Kinova modular robot arms for service robotics applications. Rapid Automation: Concepts, Methodologies, Tools, and App. IGI Global.
- Hudson, C.L., & Morell-Pacheco, G. G. (2013). Robolink: Modular Robot Arm. Retrieved from: https://digitalcommons.wpi.edu/mqp-all/2223
- Hillman, M., Hagan K., … & Orpwood R. (2002). The Weston wheelchair mounted assistive robot. Robotica.
- Toyama, H., Kawamoto, H., Sankai, Y. (2019). Development of Cybernic Robot Arm to realize Support Action cooperated with Hemiplegic Person's Arm. IEEE Conf on Engineering in Medicine and Biology Society (EMBC).
- Alqasemi, R., Dubey, R. (2007). Maximizing Manipulation Capabilities for People with Disabilities Using a 9-DoF Wheelchair-Mounted Robotic Arm System. IEEE 10th International Conf on Rehabilitation Robotics (ICORR).
- Campeau-Lecours, A., Maheu, V., Lepage, S., Lamontagne, H., Latour, S., Paquet, L., Hardie, N. (2016). JACO Assistive Robotic Device: Empowering People With Disabilities Through Innovative Algorithms. Rehabilitation Engineering and Assistive Technology Society of North America (RESNA) Conf.
- Statistics Canada (2013). Disability in Canada: Initial Findings from the Canadian Survey on Disability.
- Arim, R. (2012). A profile of persons with disabilities among Canadians aged 15 years or older. Stat Canada.
- Choi, Y.S., Deyle, T., Chen, T., Glass, J.D. & Kemp, C.C. (2009). A List of Household Objects for Robotic Retrieval Prioritized by People with ALS. IEEE 11th International Conf on Rehabilitation Robotics.
- Matsumoto, Y., Nishida, Y., Motomura, Y., Okawa, Y. (2011). A concept of needs-oriented design and evaluation of assistive robots based on ICF. IEEE International Conference on Rehabilitation Robotics (pp. 1-6).
- Brown, T. (2009). Change by design, 1-5.
ACKNOWLEDGMENTS
This work was supported by the Natural Sciences and Engineering Research Council of Canada (NSERC). Thanks to Cassandra Gélinas-Trudel and François Vézina-Paquette for their participation in the preliminary design. Thanks also to Amy Systems for providing a CAD of their wheelchair, used in Figures 1, 7 and 8.