Lucas LACHAT, Gisela CERRON, Mila EVARD, Dounia HASSAR
HE-ARC Industrial Design Engineering
Probleme statement / Research question and background
1. INTRODUCTION
1.1 Project presentation
Alfaset, a Swiss foundation that employs people with mental and physical disabilities, along with IRCR (Red Cross), created the social initiative Rehab Impulse which aims to design sustainable and high-quality products for mobility-enabling assistive technology. The targeted products are designed to allow people with physical disabilities to reach their full potential in society.
The current prosthetics supplied by the IRCR are esthetics silicone hands -five colors are available- or split hooks that operate with a harness system. This last consists of a strap going over the shoulder that transmits the needed force to the terminal device through a control cable.
Rehab Impulse mandated us, four undergraduate students in Industrial Design Engineering in HE-ARC (Switzerland) to design a mechanical prosthetics hand for person-amputee in mined countries or remote areas using the same harness system. Thus, we were asked to re-design the terminal device according to the following specifications: low cost, producible, sustainable, for adult's hands, minimum opening width: 2.75 inches.
2. RESEARCH
2.1 State of art
We first gathered information about the existing products and did a reverse design of the split hook to have a global vision of the product and identify the concepts that are more likely to work for our purpose.
2.2 Users
Then, we identified the three users that will interact with our device: the manufacturer Alfaset, the provider IRCR, and the final user, an amputee person. They all have distinct profiles, tasks, needs and constraints as follows:
- Alfaset: Manufacture and assemble the products at a cost as low as possible, while supervising their employees.
- CICR: Set up and replace prosthesis on site with local resources depending on the patient need.
- Final users: Living in different environments and cultures and lacking a part of their body for different reasons.
Methods/Approach/Solutions Considered
3. METHODS
3.1 First specifications
We made a draft of the specifications according to the mandate and user needs before completing it with a dimension focusing on Nielsen's concept of acceptability. This means that we take into account both the mechanical constraints/features and human factors.
3.2 Ergonomic and anthropotechnologic approach
To improve these specifications, we use an ergonomic and anthropological approach. Indeed, we identify final user's expectations and issues by contextualizing the request through interviews and scenarios regarding their daily life.
3.3 Relevant specifications
Thanks to this user-centered approach, we spotted typical actions the prosthetics should perform, which leads us to the unescapable feature the prosthesis should have: hold an object.
4. SOLUTIONS CONSIDERED AND INTERMEDIATE PROTOTYPES
We sketched solutions, selected the most relevant ones, and suggested them to our interviewers and mandators. The outcome was to consider a prosthetics with an operational part and an esthetic one focusing on the following items:
Structure:
- Designing the structure with three fingers as a mean to have a claw and a hook.
- Ensure a power grip between 10 to 100 N.
Esthetic:
- Designing a shell looking like a real hand.
- Seeking for an injectable, wear resistant, sustainable, washable, tenacious, fireproof and with a ride range of colors material.
4.1 Intermediate prototypes
We have prototyped three types of framework and tested them by holding specific objects that are linked to specific scenarios such as pouring water in a bottle, writing, zipping etc… While testing the operational effectiveness, we have measured the maximum power grip of each prototype to determine what type of configuration best fitted the required specifications.
The results showed us that the framework should have two articulated fingers as a gripper and a third one more distant, fulfilling the roles of support point and hook.
- The two articulated fingers must be slightly curved and perfectly facing each other.
- The third finger must be curved to ensure the hook's feature (holding light objects without using the harness system).
- The shell must have good friction properties.
Description of Final Approach and Design
5. DESIGN
Midas, our mechanical prosthetic, has been developed according to the specifications and results of our prototype's tests. Indeed, it has two distinct parts: The operational structure and the outer shell ensuring the human factors of acceptability.
5.1 Structure
The structure is a non-stigmatizing split hook prothesis thanks to the three main elements: The index finger, the thumb, and the little finger.
The thumb, which is connected to the control cable, rotates around the index finger when the user makes a shoulder movement with the harness and the third finger is a curved static element. All the elements of the structure are classified in the following table:
Piece name | Function | Link | Material | Manufacturing | Advantages |
---|---|---|---|---|---|
Main structural rod | Main fixed component for the structure | Screwed into wrist unit | Stainless steel rod | Bent | High yield strength, the bending avoiding deformations |
Thumb | Moving part to grab objects | Rotating on the index | Aluminum sheet | Laser cut | Cheap and easy to machine |
Index finger | Fixed part | Bolted to the main rod | Aluminum sheet | Laser cut | Cheap and easy to machine |
Retainer screw | Wrist interface | wrist | Stainless steel | Bought | Readily available and cheap |
Double screw thread | Wrist interface | Screw to the forearm | Stainless steel | Bought | Readily available and cheap |
Spring | Keeps the tension in the thumb | Between the thumb and the little finger | Spring steel | Bought | Readily available and cheap |
Plain bearing | Reduces friction in | Fixed in the index | Polymer | Bought | Readily available and cheap |
5.2 Esthetic
The esthetic part is only made of three elements: the upper and lower shells made by injection molding and the thumb, overmolded. The thumb is designed in a way to protect the structure from dust and water without compromising the rotation.
They are made of polypropylene because it is economic, light, it allows a wide range of colors that match different skin tones, and it is already manufactured by the producer Alfaset.
In addition, silicone patches are glued to each fingertip of the lower shell, because this material has quite similar friction properties as human skin.
Cost
6. COST TO PRODUCE AND EXPECTED PRICING
6.1 Cost to produce
To estimate the cost to produce, we first need to assess the cost price of a raw material, manufacture and indirect cost. It adds up to 67 CHF (Swiss Franc CHF approximately 72.06 USD) for a serie of one hundred pieces.
- Cost of raw material
- Is estimated to 23.50 CHF (=25.28 USD) according to the cost of each following elements for a serie of one hundred (Swiss suppliers).
- Aluminium sheet: 10 CHF (=10.76 USD)
- Stainless steel rod: 5 CHF (=5.38 USD)
- Steel tube : 3 CHF (=3.23 USD)
- Plain bearing: 1.40 CHF (=1.51 USD)
- Fastening elements: 1 CHF (=1.08 USD)
- Spring :2.50 CHF (=2.69 USD)
- Polymers : 0.5 CHF (=0.54 USD)
- Cost of manufacture
- Is estimated to 36.5 CHF (=39.26 USD) for a serie of one hundred pieces per year.
- Laser cut : 5 CHF (=5.38 USD)
- Bending : 2 CHF (=2.15 USD)
- Machining : 20 CHF (=21.51 USD)
- Plastic injection : 4.5 CHF (=1.08 USD)
- Assembly : 5 CHF (=5.38 USD)
- Indirect cost
- Is estimated to 7 CHF (=7.53 USD) taking into account the salaries, rent, marketing etc…
6.2 Expected pricing
The expected pricing is 77 CHF (=82.82 USD) as it is the sum of the cost to produce and gross profit (estimated to 10 CHF which is 10.76 USD).
Significance
7. SIGNIFICANCE
Midas means a lot to the users and to our project group.
The final users, people with an amputated arm, face significant problems in their daily-life and Midas intends to reduce them. For this purpose, it has been designed with amputees and for them, and takes into account all their constraints and needs so as to significantly improve their daily life. For instance, we noticed that the current prosthesis were not convenient because they do not match the environmental issues (the elements are not interchangeable or need to be recharged in remote areas) or the user's expectations (their hook appearance is stigmatizing). So we countered these disadvantages by designing a prosthesis looking like a real hand, completely mechanical and interchangeable at site.
The prosthetics hand has also been designed for the first user: Alfaset. Their main goal is to produce and assemble the terminal device at low cost. The assembly is easy and the machining uses common materials and methods known by the foundation.
Midas also means a lot to our project group because we discovered a real human issue that we were eager to solve. Designing this device was our rewarding way to contribute to the life improvement of people with disabilities. In terms of skills improvement, we put into practice all our undergraduate skills in engineering (especially in Industrial design engineering). But we also left our comfort zone and challenged ourselves by participating in this contest and learning how to manage a project and work in a group.
Outcome
8. OUTCOME
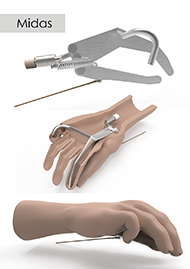
We presented our final approach to our mandator from Alfaset, a prosthetist from the IRCR and the amputees with whom we did the interviews. They were delighted by the solution and suggested us some minor changes (such as the diameter of the rod) so we can constantly tweak our design.
9. FUTURE PROSPECT
We will run finite elements analysis in order to simulate the prehension, check that the structure will never exceed the yield strength, and make sure that the shell has the expected fracture toughness and fatigue strength.
We will thereupon realize a prototype at scale and have it tested by the final users, using an on-going process to constantly improve the design.
Feedbacks of the users are essential as we are providing technical solutions while being concerned about putting the human being at the heart of the project and designing a prosthetics hand that best fits all the user's needs.
Midas looks like a hand but Midas is more than a hand for arm amputee people.
References
- Alan M. Jette, Carol Mason Spicer, and Jennifer Lalitha Flaubert, National Academies of Sciences, Engineering, and Medicine.
- "The Promise of Assistive Technology to Enhance Activity and Work Participation ", 2017.
- Joseph T. Belter, Bo C. Reynolds and Aaron M. Dollar, IEEE Senior Member.
- "Grasp and Force Based Taxonomy of Split-Hook Prosthetic Terminal Devices", 2014.
- Clinique romande de réadaptation SUVA "Vivre après une amputation ", 2017.
Acknowledgements
We would like to thank the teaching staff who supervised our project.
As well as the Alfasets members who participated in the project including the referent,R.Ayer.
We also want to thank the ICRC contact prosthetist Jean-Pierre Schepens and all the external people who participated in this project.
Alan M. Jette, Carol Mason Spicer, and Jennifer Lalitha Flaubert, National Academies of Sciences, Engineering, and Medicine.
"The Promise of Assistive Technology to Enhance Activity and Work Participation ", 2017.
Joseph T. Belter, Bo C. Reynolds and Aaron M. Dollar, IEEE Senior Member.
"Grasp and Force Based Taxonomy of Split-Hook Prosthetic Terminal Devices", 2014.
Clinique romande de réadaptation SUVA "Vivre après une amputation ", 2017.
Dr. Carole Baudin
Professor in anthropology and ergonomics design
Haute Ecole de l'Arc in Neuchâtel
Espace de l'Europe 11, CH-2000, Neuchâtel, Switzerland
Dr. Anne Polikeit
Professor and responsible of the faculty in Industrial Ergonomics Design
Haute Ecole de l'Arc
Espace de l'Europe 11, CH-2000, Neuchâtel, Switzerland
Roger Ayer
Manager Advanced Operations Stryker
Alfaset Foundation
Rue des Terreaux 48, CH-2300, La Chaux-de-Fonds, Switzerland