LeTourneau University
Problem Statement/Research Question and Background
Wheelchairs offer many benefits in addition to added mobility, but these benefits can be lost during travel in vehicles such as taxis and buses, especially in developing nations. This situation is made worse by the fact that due to the added time and hassle involved with stowing a wheelchair, many taxi drivers will avoid offering support to groups that include a member who uses a wheelchair.
This problem was recently noticed by Beeline, a nonprofit manufacturer and distributer of wheelchairs in Guatemala. Faced with this difficult situation, Beeline partnered with LeTourneau University's Frontier Wheelchairs senior design team to design and build a prototype quick release feature for their wheelchair seats.
The chief specifications for the quick release feature were that it needed to be easily manufacturable by Beeline, sturdy while attached to the wheelchair, and easy to attach and detach. Other desires were that it would cause no damage to the seats it would be placed on, be of a light weight, and use materials which would be easy to purchase in undeveloped areas.
Methods/Approach/Solutions Considered
When designing this product, manufacturability, durability, and usability were deemed to be of paramount importance:
Manufacturing and part accessibility: This project was designed in cooperation with Beeline Wheelchairs, a company located in Guatemala. When designing our product, the resources and manufacturing processes available to them were taken into account leading to multiple conversation about the availability of parts. The strength of materials, availability, and cost must all be considered in our design.
Designing for durability: This device is designed to be used in low-income countries where paved roads may be uncommon. Thus, our product needs to be durable. The quick release mechanism that we designed must be capable of providing a strong, durable connection between the seat and the rest of the wheelchair. The Quick Release Seat must be safe to use but also be able to withstand wear and tear.
Creating an easy-to-use product: Our third major design consideration was making the attachment and detachment of the seat as simple and efficient as possible. Our iterative design process included testing for ease of use.
Taking all of these into consideration, the project was started with a brainstorming session where each member presented multiple solutions. These solutions were evaluated and the best features were combined leading to two concepts which were developed in parallel. In the end, a highbred of the concepts was suggested which became the basis for the first prototype. From this point, the project followed an iterative process of prototyping followed by evaluation.
Description of Final Approach and Design
Our initial prototype involved two interlocking pieces, one connected to the bottom of the seat (seat base) and one attached to the wheelchair (base retainer), both of which were made from wood. These pieces are aligned using a metal tab and slot and are locked in place with a latch.
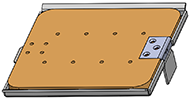
After meeting with Beeline, we reviewed our design using their feedback. Iteration upon our initial design led to reduced thickness of the parts and using sheet metal in place of wood for the base retainer. The base retainer can be cut out of one piece of 1/8- inch steel and bent to shape using tools available to Beeline. Review of our design also switched the location of the metal tab from the wheelchair portion to the base of the seat. This ensures a smooth surface on the bottom of the seat which allows it to be placed on surfaces and seats without damaging them.
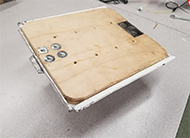
We further iterated upon our design to improve aligning and attaching the seat to the retainer. This was done by reducing the size of the metal tab and adding flared wings to the retainer to guide the seat in.
Outcome (results of any outcomes testing and/or user feedback)
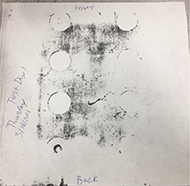
The quick release seat has undergone drop testing to test the durability of the seat and latch. In five hours, the seat was dropped approximately 5000 times. As a modification of the ISO curb drop test, the entire wheelchair was lifted by the seat and then dropped 2 inches. Carbon paper was placed between the seat and base to observe the weight distribution. As shown in Figure 3, the front side has slightly more weight applied to it than the back side. It was noticed that one of the bolts was imprinting the carbon paper significantly more than the others. This was because the bolt was not screwed in completely. The weight was concentrated in the center.
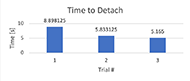
Sixteen students who are unrelated to this project have tested attaching and detaching the quick release seat from the wheelchair. Figure 4 shows the time in seconds to unfasten and remove the seat. As the user gets more experience, the time decreases. Figure 5 shows the time to reattach and fasten the seat. This time also declines significantly as the user gains experience. The students were able to use the product more easily when the wheelchair was secure and stable, and many of them stated that brakes would have made the process simpler.
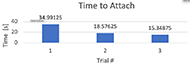
In Figure 6, the students have answered questions after attaching and detaching the seat three times regarding size, ease of locking, ease of alignment, and ease of detachment. The higher the score is, the easier it is to lock, align, and detach. Overall, the students gave the seat positive feedback.
Cost (cost to produce and expected pricing)
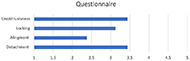
The budget goal for this project was to make it as inexpensive as possible because this product has been specifically designed to be built and used in low income countries. It cost $41.12 for the materials to produce the final prototype as detailed in Table 1.
Prototype cost | Production cost | |
---|---|---|
Metal | $18.05 | $8.84 |
Plywood | $10.20 | $0.90 |
Latch | $3.81 | $3.81 |
Bolts and nuts | $9.06 | $1.45 |
Total | $41.12 | $15.00 |
This cost estimate does not include engineering development time, consultations with customers, and labor. The plywood, sheet metal, bolts, and nuts were purchased in bulk. However, only small sections were used to produce the prototype. Thus, the prototype is estimated to be more expensive than the product will cost in mass production. Expected material pricing for production is listed in Table 1. We estimate our prototype took 4 hours to build from the drawings. But we estimate that time will come down rapidly with learning curve, such that the 20th unit would take 1 hour. Assuming $2/hr, which is above minimum wage in Guatemala, this would result in labor cost of $2/unit. So total cost with material and labor of the 20th unit would be $17. Since the wheelchairs are provided "at cost" through donations, the price will equal the cost.
Significance
The current prototype has minor adjustments that are being addressed and will be implemented into a final design to be delivered to Beeline along with CAD drawings and manufacturing methods. This design, due to its affordability and ease of use, will be able to be incorporated into Beeline's Honeybee wheelchair for use in Guatemala where a study found 31% of households have someone with a disability [1].
Once incorporated, travel will be much easier for people using these wheelchairs. The quick-release wheelchairs can be easily dismantled for stowing in the trunks of cars and taxis. Alternatively, people who need their wheelchair seats for spinal support will be able to use their supportive seats resting on the seats of cars, taxis and buses, utilizing existing seat belts. This device will make this wheelchair more useful to more people.
References
- C. Dionicio, S. Grech, I. Mactaggart, J. Naber, A. R. S. de Barrios, G. Rota, S. Polack 2016, Guatemala National Disability Study, 22 March 2021, <https://www.cbm.org/news/news/news-2017/guatemala-national-disability-survey-endis/>.
Acknowledgements
The product design, fabrication, and testing were conducted in the 2020-21 Senior Design class in the School of Engineering and Engineering Technology at LeTourneau University. A special thanks to Professor Norman Reese for mentoring the design team over the course of the project. This project would not have been possible without the guidance and clinical feedback of Beeline Wheelchairs, of Sacatepequez, Guatemala.