Knack: A Low-Cost 3D Printed Prosthetic Hand Using Thermoplastic Polyurethane
Niell Gorman, David Edquilang, Jeff Feng
University of Houston Industrial Design
1) Problem Statement/Research Question and Background
More than two million Americans currently live with limb loss, while an estimated 12,500 new upper limb amputations occur in the US every year [1]. The cost of the average commercial functional prosthetic hand is between $10,000 and $30,000 [2], which can be out of reach for many low-income or uninsured amputees. This may be a contributing factor to the comparatively low usage of prosthetics among upper limb amputees, just 56% compared to 84% for lower-limb amputees [3]. Based on these statistics, it may be concluded that there exists a significant need for low-cost functional prosthetic hands. Several open-source hand designs exist to address this need, utilizing fused deposition modelling (FDM) 3D printing to allow for the decentralized fabrication of functional prostheses on widely available consumer-grade printers. However, many currently available 3D printed hands suffer from durability issues and lack realistic flexibility due to their exclusive rigid polylactic acid (PLA) plastic construction. There is also a lack of available data on their user acceptance and durability [4], which suggests there is a gap between the design intent and real-world performance of such printed devices. Thermoplastic polyurethane (TPU) material is an elastic material that can be 3D printed on most FDM printers. Strong, skin-safe, and available in a variety of durometers, TPU is ideally suited for the fabrication of compliant mechanisms. An improved hand applying the benefits of compliant design and TPU construction to simplify the hand's mechanical structure and increase durability would represent a significant advancement to the current offering of 3D printable hand prostheses. This hand would be validated through user testing to prove its functionality in actual use.
2) Methods/Approach/Solutions Considered
To create a more dexterous, realistic, and flexible prosthetic hand, a biologically inspired design approach was used. Literature review was conducted into the musculoskeletal structure and biomechanics of the hand, with particular focus on the finger joints. This study provided key dimensions, range-of motion measurements, as well as inspiration for a more naturalistic hand mechanism. Several conceptual approaches to the mechanical design of the hand were tested. Initially, compliant TPU "living" hinges were used for finger articulation instead of mechanical, rotational hinges. While this effectively reduced the number of components and increased functional dexterity, it left large gaps between the finger segments. The necessary thinness of the hinges meant they did not possess enough elastic memory to extend the hand when not being actively flexed using the control cables. A hybrid design was needed to combine the mechanical benefits of the conventional hinge with the dexterity and simplicity advantages of the living hinge. Sufficient return force was achieved with the use of TPU springs inspired by the ligaments of the hand. Many prototype iterations were used to fine-tune the thickness, closure, and return force of the springs.
3) Description of Final Approach and Design
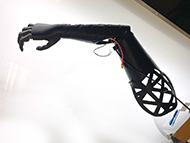
The final approach uses a modular finger design with hybrid rigid/compliant PLA and TPU construction. The fingertips are constructed entirely from TPU, featuring compliant, textured finger pads for grip and an integrated return spring. The proximal phalanges are printed from rigid PLA plastic, with two rotational snap-fit hinges articulating each digit, save for the thumb, which features one hinge. Separate TPU springs slide into the PLA below the second knuckle. Each finger locks into the palm assembly by an interference fit with twin hooks, providing a high-strength interference fit that allows the hand to be assembled without hardware or glues. Control cables are routed through channels in the finger, contoured to minimize friction and maximize grip force. The palm consists of two pieces, a rigid PLA housing which holds each finger and joins to the wrist, and a textured TPU palm for gripping objects. Aesthetically, the palm and fingers are contoured to give the hand a sleek and realistic look. A prosthetic arm and rotational wrist were also fabricated using PLA, so that the hand could be fit to a user with a transhumeral amputation. The forearm encloses a linear actuator, powered by an 11.1 V rechargeable battery, that pulls the control cables to open and close the hand.
4) Outcome (Results of any outcomes testing and/or user feedback)
User testing was conducted in collaboration with occupational therapy staff at Quentin Mease Hospital in Houston, Texas. Through an ongoing research relationship, a patient was identified in need of an upper-limb prosthesis. Previously, the patient was using a rigid arm hand-crafted by occupational therapists from thermoformed plastic, aluminum bar stock, and rubberized wall hooks. Since this prosthesis could neither close to grip objects or bend at the elbow, a 3D printed functional prosthetic hand and arm would greatly improve his ability and quality of life. Through several rounds of measurement and test-fitting, the design was adapted for the specific needs of the user. While final testing and fitting of the device is ongoing currently, the user reports to be satisfied with the fit and performance of the prosthesis. Additionally, the occupational therapy staff provided very positive feedback, as the 3D printed hand provides an affordable, functional, and dependable option for amputee patients who lack funds for any type of prosthesis.
5) Cost
The complete hand uses less than $15 of PLA and TPU material. Internal motorization components are the most expensive portions of the assembly, with the linear actuator priced at $70, the battery at $18.50, and control switch at $8. However, these electronic components are only necessary for a user with a transhumeral amputation, and a body-powered tensioner system could be substituted for use by transradial and hand amputees. Ideally, the files to print this hand design would be open-source, available free of charge. However, distribution options have yet to be explored.
6) Significance
The resulting hand, Knack, features several advancements over the current offering of 3D printed prosthetic hands. Firstly, the number of components used is drastically simplified, with only 20 parts comprising the hand. This is a halving of complexity compared to one of the leading 3D-printable hands which features 41 discrete components, reducing fabrication time and cost. The design is also entirely 3D-printable, requiring no extra hardware or adhesive to assemble unlike many open-source prostheses. Every part of the hand itself attaches via an interference fit, with minimal cleanup needed between printing and assembly. The compliant TPU fingertips are more durable than rigid ones and possess a lifelike softness and grippy texture that rigid designs lack. The TPU springs provide strong, reliable return force without the need for elastic bands. Finally, Knack is realistic in its appearance, modeled after the human hand's natural resting position.
References:
- Industrial Safety and Hygiene News. https://www.ishn.com
- Amputee Coalition. https://www.amputee-coalition.org
- Raichle, K., Hanley, M., Molton, I., Kadel, N., Campbell, K., Phelps, E., Ehde, D., Smith, D.: Prosthesis Use in Persons with Lower- and Upper-Limb Amputation. In: Journal of Rehabilitation Research and Development, pp. 969. Department of Veterans Affairs, Washington D.C. (2008)
- Kate, JT., Smit, G., Breedveld, P.: 3D-printed upper limb prostheses: a review. In: Disability and Rehabilitation: Assistive Technology, pp. 300--314. (2017)
Acknowledgements:
Faculty Mentor: Jeff F. Feng
Occupational Therapy Collaborator: Florence K. Brown, OTR