Sarah Vigneault1,2
, Thierry Laliberté
1
, Simon Latour
2
, Véronique Flamand
2
, Alexandre Campeau-Lecours
1,2
1
Department of Mechanical Engineering, Laval University (Quebec City)
2
Centre of Interdisciplinary Research in Rehabilitation and Social Integration (Cirris), CIUSSS de la Capitale-Nationale (Quebec City)
ABSTRACT
This paper presents the industrial design of a mechanical assistive eating device which aims to stabilize the motion of people living with movement disorders. Movement disorders are usually a result of neurological disorders, such as cerebral palsy, stroke, muscular dystrophy or dystonia leading to upper limb impairments (muscle spasticity, loss of selective motor control, muscle weakness or tremors). The proposed assistive eating device is designed to allow people living with movement disorders, more precisely abrupt movements such as spasms, ataxia or dystonia, limited hand or arm mobility, to eat independently. A review of currently available assistive eating devices is first presented, followed by previous iterations of the proposed assistive eating device. The industrial design of the device, aimed at improving aesthetics (for acceptability considerations) and reducing cost (for affordability purposes) is then presented, followed by the mechanical design to better meet the needs of the users, such as improving the static balancing, the stabilization for involuntary movements, the handle, the utensil attachment, and the plate mechanism fixation.
INTRODUCTION
Many people live with neurological disorders such as cerebral palsy, stroke, muscular dystrophy or dystonia experience upper limb impairments (muscle spasticity, loss of selective motor control, muscle weakness or tremors, limited hand or arm mobility) that limit their ability to eat independently. The ability to eat without the assistance of a caregiver is an important aspect of independent daily living [2] and this situation is problematic in a context of ageing population and labor shortage [1]. In this section, we present the currently available assistive eating devices that enable users to eat independently, and the iterations of our assistive eating device.
Currently available assistive eating devices
The first group of devices are adapted utensils. Basic solutions include adapted handle shapes and bendable utensils. More recently, anti-tremor utensils and self-levelling spoons have been commercialized. Liftware [www.liftware.com] offers two types of electronic handles. Whereas the Liftware Steady™ is designed to help people with hand tremors by using an advanced sensor and motor-based tremor cancellation technology, the Liftware Level™ enables independent eating for people with limited hand or arm mobility by using an advanced sensor and self-levelling technology. ELISpoon [www.elispoon.com] has a mechanical self-levelling solution with no electrical components and is more affordable than the aforementioned solutions. Scientific literature [1] and discussions with occupational therapists have shown that these solutions may be suitable for users with contractures or living with tremors, but do not address the needs of people living with abrupt movements such as spasms, ataxia or dystonia.
The second category includes mechanical assistive devices designed to reduce the effects of abrupt movements. For instance, the Nelson [www.focalmeditech.com] and the Neater Eater [www.neater.co.uk] are equipped with dampers in order to reduce the amplitude of abrupt movements and reduce the effect of spasms.
The last group covers robotic dining aids such as the Obi dining device [www.meetobi.com], iEAT Feeding Robot [www.assistive-innovation.com] and Winsford Feeder [4]. They are designed to feed the users semi-autonomously. These devices retail in the range of USD 8,000 to USD 50,000, which is expensive for the target population. Also, robotic aids require complex actions and offers insufficient adaptation to the user's needs.
Occupational therapists, caregivers and potential users agree that there is a gap between currently available assistive eating devices for people living with movement disorders linked to spasticity, spasms, ataxia and dyspraxia. The first reason is the lack of product functionality: expensiveness (mostly robotic systems), low ergonomics, lack of freedom of movement, strong demand for the user's strength to lift the device's weight (not intuitive), or unsuitability with the user's capacity. Also, available products are mostly mechanical devices that have mechanical limitations compared to devices with electronic features. The second reason it that robotic systems may be well suited for people living with tetraplegia, since they require only a small range of motion and strength to be operated by the user, but they are far from optimal for people living with motion disorders. Indeed, from an occupational therapy point of view, taking advantage of only a small part of the user's available motor function is not a viable long-term solution. In short, for people living with movement disorders linked to spasticity, spasms, ataxia and dyspraxia, there are no solutions on the market that can perfectly meet their needs.
Previous designs
First design: Five-bar linkage mechanism
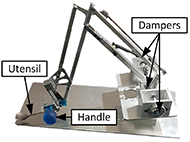
Figure 1 shows a five-bar linkage mechanism with three degrees of freedom (DoF) (enabling three translational Cartesian movements) and is detailed in [3]. The five-bar linkage allows the spoon to remain horizontal at all times. Three dampers, placed at the base of the mechanism, allow for the damping of abrupt movements. The mechanism is also statically balanced which enables the mechanism to support its own weight. Different handle shapes, such as a ball or cylinder are available. The handle rotates on itself to help people with limited hand or arm mobility. An important feature is that a mechanism allows for an amplification of the user's vertical movement to raise the utensil, thus requiring shorter vertical movement to bring the utensil to the mouth. The utensil attachment is designed to be flexible for safety considerations. The main disadvantage of this design is the surface area used on the table, the complexity of the design (for machining considerations) and the fact that it is difficult to attach to a table.
Second design: Serial mechanism
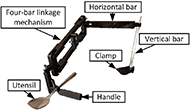
The proposed serial mechanism has three DoFs (enabling three translational Cartesian movements). The architecture consists of a vertical bar fixed to the table with a clamp, followed by a horizontal bar and a four-bar linkage mechanism, as shown in Figure 2. The four-bar linkage mechanism is used to ensure that the spoon remains horizontal at all times. There are three dampers (not shown in Figure 2), one on each joint, to reduce the amplitude of abrupt movements. Two extension springs are attached to the four-bar linkage mechanism (not shown in Figure 2) to statically balance the device. Although this design has the potential to reduce machining costs and is easy to attach to a table, there are two main drawbacks that limit the acceptability of the solution since they have not been optimized in the design: machining costs and aesthetics.
These discussions led our team to the design of a new assistive eating device [2,3] aimed to help people living with motion disorders (spasticity, spasms, ataxia and dyspraxia) to eat independently. The principle was to focus on mechanical innovations to answer users' and stakeholders' needs while reducing cost as much as possible as high cost is the main limiting factor in the adoption of assistive technologies [5,6]. The new mechanism is designed to be affordable, adaptable to the user's needs, usable without any assistance, and easy to use.
OBJECTIVES
The objectives of the new device are: 1) to perform an industrial design iteration to improve aesthetics, which is very important for acceptability considerations; and 2) to revisit the design to reduce the cost of the mechanism, all the while maintaining and improving the device's functionalities.
SUMMARY DESCRIPTION
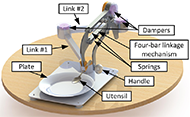
The proposed mechanism, which is designed to be mounted on a table or a table tray, is shown in Figure 3. Although the five-bar linkage mechanism provides a better damping of the movements, the potential of the serial architecture was too important to be neglected. For this reason, the new device has the same architecture as the serial mechanism. The user operates the device by grasping and moving a handle from the plate to the mouth. The optimization of the link's length allows the user to reach the plate's entire range. The four-bar linkage mechanism allows the utensil to remain at the same orientation at all times. There are two types of handles (detailed in the mechanism design section). Dampers are placed on each joint and allow for the stabilization of the user's motion by reducing the amplitude of abrupt movements while two springs statically balance the system. The mechanism is designed to fit both right and left-handed users.
INDUSTRIAL DESIGN
Aesthetics
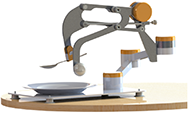
Figure 4 presents a first iteration of the industrial design based on the serial mechanism of the prototype. According to potential users, the prototype needed to be inconspicuous, space-saving and easy to transport. The first two links are assembled in a stair-like manner to reduce the space occupied by the mechanism on the table and to allow for a better aesthetic to the design. The prototype's colour is neutral and can be personalized (e.g., various colours, stickers). Cutting point hazards were taken into consideration in the aesthetic design for safety purposes by avoiding the edges of two moving parts moving across each other.
Manufacturing cost
The materials were chosen to withstand the forces applied to the system and to reduce the manufacturing cost of the product. Most parts are made from aluminum to resist operating loads: the first two links are made from aluminum sheet metal, and the four-bar linkage mechanism as well as the mechanisms' base are made of standard aluminum plates. Standard materials such as aluminum plates and sheet metal, as well as standard hardware like dampers, spring, rubber pieces, bushings and boltswere chosen to limit the complexity in the manufacturing of the product without compromising its functionality. The design also aims to duplicate parts instead of creating similar parts to considerably reduce the manufacturing cost.
MECHANISM DESIGN
Dampers
FDT-47 dampers are used because they are the most effective for the needs of this application. They reduce the amplitude of abrupt movements by providing a force proportional to the velocity and opposing the motion [7].
Static balancing
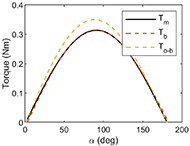
The static balancing depends on the weight, center of mass and position of the fixed points of the springs. Therefore, calculations must be made to find the correctly balanced parameters for the system. Figure 5 shows the torque resulting from the mechanism's weight (Tm) versus the required torque to balance (Tb) and overbalance (To-b) (explained later) the system. Based on the data from the curves, two LE 026C 14S springs have been chosen to adequately balance the mechanism. They are attached on each side of the four-bar linkage mechanism at specific positions. Two balancing modes have been added to the previous versions: balanced and over-balanced. The balanced version supports the mechanism's weight so the user can move the utensil without compensating for the mechanism's weight. The over-balanced version, obtained by simply changing the spring attachment point, overbalances the mechanism. Thus, a part of the user's movement is automated in order to limit the effort provided by the users as they only have to pick up the food on the plate and let the mechanism rise by itself to the mouth level.
Handle attachment design
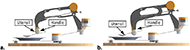
Figure 6 shows the two available types of handles. The user chooses the type of handle that best fits their needs or preferences. Figure 6a shows the handle type that is attached to the four-bar mechanism with an offset relative to it, in order to be aligned with the utensil. The resulting behaviour of this attachment design is that the required upward handle movement amplitude to generate the same spoon vertical movement is reduced by 50% [3] compared to a generic movement from the table to the mouth level, and meets the needs of users with muscle weakness, and limited hand or arm mobility. Figure 6b shows the handle attached at the end of the mechanism and to the utensil so the user is able to rotate the spoon. Users that have the ability to reach their mouth easily can use this type of handle to improve movement fluidity and maintain the damping purpose of the mechanism.
Compliant utensil attachment design
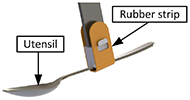
Figure 7 presents the compliant utensil attachment designed to avoid any injuries from involuntary movements while the utensil is near the user's mouth. The utensil can be attached by pulling a rubber strip, placing the utensil and putting the end of the rubber strip in place. The rubber material reduces the amplitude of the utensil's movement if any abrupt motion occurs.
Plate mechanism fixation
Four rubber suction cups are placed at each corner of the mechanism plate to attach it to the table to reduce the space occupied by the fixation it proves suitable for most tables and provides a stable base to the mechanism. For non-compliant tables, the mechanism can be attached with a clamp.
DISCUSSION AND CONCLUSIONS
In this paper, an improved industrial design of a 3-DoF assistive eating device was presented. The device aims to allow users living with movement disorders such as spasms, ataxia or dystonia, limited hand or arm mobility, to eat on their own. The objectives were to develop an improved version of the eating device from the previous designs 1) to perform an industrial design iteration to improve aesthetics, which is very important for acceptability considerations; and 2) to revisit the design to reduce the cost of the mechanism while maintaining and improving the device's functionalities. Due to its potential, the serial architecture was chosen over the five-bar linkage mechanism architecture. The redesign also includes a review of the mechanical design to better meet the needs of the users, i.e., improving the static balancing, the stabilization for involuntary movements, the handle, the utensil attachment and the fixation of the mechanism's plate. In the short term, future work includes building a prototype of the device and performing preclinical validation to assess the device's acceptability, usability and user satisfaction.
REFERENCES
[1] Ministère de la Famille du Québec. Les ainés du Québec, Quelques données récentes, Deuxième éd.; 2018.
[2] Turgeon P, Dubé M, Laliberté T, Routhier F, Archambault, P, Campeau-Lecours, A. Mechanical design of a new assistive eating device for people living with spasticity. Assistive Technol. 2020 Mar 13;1-8.
[3] Dubé M, Laliberté T, Flamand V, Routhier F, Campeau-Lecours A. (submitted). Mechanical design improvement of a passive device to assist eating in people living with movement disorders. Rehabilitation Engineering and Assistive Technology Society of North America (RESNA); 2020.
[4] North Coast Medical. (2011). Winsford Feeder. Retrieved October 9, 2019, from https://www.ncmedical.com/wp-content/uploads/2011/07/Winsford-Broch_web_0611.pdf
[5] Statistics Canada. (2013). Disability in Canada: initial findings from the Canadian Survey on Disability.
[6] Federici S, Meloni F, & Borsci S. (2016). The abandonment of assistive technology in Italy: a survey of National Health Service users. European journal of physical and rehabilitation Medecine, 52(4), 516-526.
[7] ACE Controls Inc. (2019). Rotary Dampers. Retrieved November 20, 2019, from https://www.acecontrols.com/us/products/motion-control/rotary-dampers.html
ACKNOWLEDGMENTS
This work was supported by the Natural Sciences and Engineering Research Council of Canada (NSERC) and the Fonds de recherche du Québec – Santé (FRSQ) Research Scholar under Grant #34699.