Melanie Peterson, Nicholas Gates, Jonathan Sander
Faculty Advisors: Mohamed Samir Hefzy, Ph.D., PE, ASME Fellow and Mehdi Pourazady, Ph.D.
Biomechanics and Assistive Technology Laboratory, Department of Mechanical, Industrial and Manufacturing Engineering, The University of Toledo, Toledo, Ohio 43606
ABSTRACT
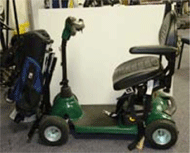
The objective of this project was to modify a standard power cart for use by a young boy, who has limited use of his legs, on a golf course. An Invacare Lynx-L3 [1], shown in figure 1, was modified in order to allow this “client” maximum independence and accessibility while providing all of the necessary features for a golf cart. To accomplish this, two main modifications to the power cart were made. The first modification was a redesign of the rotating seat to incorporate a tilting function and a safety harness. The second modification was a redesign of the front axle of the cart to change it from a three wheel design to a more stable four wheel design. An electric actuator mounted at the bottom of the seat base was used for the tilting mechanism. The design features two bar linkage on each side of the seat that allows the backrest to remain vertical while in the tilted position. The steering system developed for the front axle design includes a bracket on the steering column, tie rods and spindles. The tie rods attach to the bracket and connect it to the spindles which enable the cart to steer. New, larger off-road tires were also installed to provide the appropriate traction for maneuvering the golf course. A golf bag holder was also fitted to the cart to carry the essential golf items. The adapted golf cart is depicted in figure 2.
KEYWORDS
Adaptive Golf Cart; Power Cart; Spina Bifida; Manual Wheelchair
BACKGROUND
People with disabilities have little access to activities such as golf due to limited wheelchair accessibility or the need for assistance from other people when participating in the activity. This is unfortunate, because activities such as these can be very therapeutic for an individual, allowing them to play the sport they love. The “client”, a ten year old boy with spina bifida, loves to play golf, but has very limited access to play because he uses a manual wheelchair which cannot maneuver on a golf course. There are several adaptive golf carts on the market today, such as those available from EV Rider [2], GolfXpress [3] and SoloRider [4], but these carts are designed for adults and are difficult and unsafe for smaller people to operate. These carts are also very expensive, ranging in price from $3,990 to $9,950.
DESIGN OBJECTIVES
The objective of this project was to adapt a power cart to efficiently maneuver about a golf course and allow the user to golf while remaining seated. The main design criteria were safety, ease of use, reliability, comfort and usability.
METHODOLOGY/DESIGN
The adaptation of the power cart required adding a seat tilt function to allow for a better swinging motion for the user, and to change the cart design from three wheels to four wheels to add stability. This required the redesign of the cart seating and steering systems.
Seat Design:
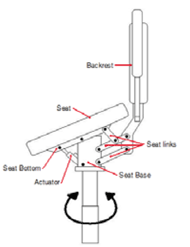
Modifications performed to the seat include the addition of a tilting function as well as a safety harness to hold the passenger securely in place while golfing. The added tilting function allows the user to golf from a position that will drop their knees and enhance their swinging motion. Electric actuator, hydraulic cylinder, and a manual lever designs were considered to actuate a linkage that would raise the rear of the cart’s seat. Using a House of Quality, the electric actuator design was chosen for its ease of use, its limited space usage, and its infinite number of inclination angles at which the user can position the seat within its motion range. This will allow the user to position the seat in the most comfortable position for them to swing from. A linear electric actuator was mounted at the bottom of the seat base and connected to the center of the rear of the seat bottom. The design of the seating system also features a parallel, two bar linkage on each side of the seat that adds stability to the seat and allows the backrest to remain vertical while in the tilted position. A diagram outlining the electric tilt mechanism is shown in figure 3.
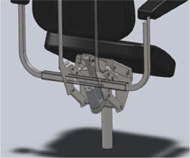
To design the electric tilt seat, a 3-D working model of the existing seat and all of its hardware was first developed using SolidWorks. An approximate tilt seat linkage was then modeled and adapted to the existing seat model. After a working assembly of the seat was created, dimensions of the various linkages were changed to produce the desired tilting motion. The actuator was then incorporated into the model. Figure 4 is a view from the back side of the seat which shows the finalized placement of the actuator.
With the desired kinematics modeled, calculations were performed to determine the maximum load that would be exerted on the actuator. To do this, the geometries of the seat base, seat bottom, and linkages were analyzed and the pieces were approximated as rigid beams. Using the various angles of the linkages and actuator relative to the seat base and assuming a rider weight of 250 pounds, the maximum rider weight for which the Lynx L-3 is rated, actuator reactions were calculated throughout the tilting range of the seat. Rider weight was approximated as a concentrated force acting at the center of the seat. This process was iterative as calculations had to be performed based on geometries that would accommodate readily available actuators with a predetermined load rating and extension range. The maximum calculated actuator force was 93 pounds at an inclination angle of zero degrees. The actuator that was eventually chosen is manufactured by Firgelli Automations and provides two inches of extension (2” stroke) while supporting loads of up to 150 lbs.
After determining an appropriate seat linkage and actuator selection, analysis was performed on the seat’s various components. First, the shear stresses and bearing stresses were calculated for the pins on which the seat linkages pivot. Stresses were calculated using the maximum reaction force of 209 pounds calculated at the main pivot point between the seat bottom and the base. From the results of these calculations, the maximum shear stresses and bearing stresses were computed for the pivot pins and actuator mounting bolt. The lowest factor of safety found for the pivot pins was 14.571 and the lowest for the actuator mounting bolt was 22.174.
Next, Finite Element Analysis (FEA) was performed on various components of the seat. An assembly was made of the base and seat bottom and included a solid link to simulate the actuator. A 250 pound load was applied to the seat bottom and the analysis was used to verify the hand calculations for actuator load. The load calculated by the FEA analysis for the fully retracted actuator position was 93.1 pounds. When compared to the hand calculated value of 92.6 pounds, there is only a 0.54% difference. For the fully extended actuator position, the FEA analysis yielded a load of 72.9 pounds on the actuator compared to 70.2 pounds calculated by hand, which represents only a 3.7% difference and verifies the accuracy of the hand calculations.
The next analysis that was performed was on the new seat bottom. This is the piece that the actuator pushes on to tilt the seat. This piece was designed using 11 GA (.120 in) AISI 1008 carbon steel sheet. For the analysis, the seat bottom pivot point and the actuator mounting hole were both constrained as fixed hinges. This constraint allows rotation about each hole but does not permit translation in any direction as would be the case when the actuator is not moving. Then, a 250 pound load, representing the weight of the rider, was distributed across the top of the piece. The seat bottom was analyzed in the fully retracted actuator position as this would be the highest stressed case. A minimum factor of safety for the piece was calculated as 3.32 and occurred just above the main pivot holes.
In addition to the seat bottom, FEA analysis was also performed on the seat base. This piece, which fits into the original seat mounting post, serves as the attachment point for the seat linkages as well as the actuator. It is constructed from 11 GA AISI 1008 carbon steel sheet and also includes the pivot point for the seat bottom. In the analysis, the mounting post, which allows the base to rotate about its attachment post on the cart’s frame, was constrained as fixed geometry, preventing it from rotating or translating in any direction. Then, the previously calculated loads (maximum calculated force of 93 lbs. acting on the actuator when fully retracted and maximum reaction force of 209 lbs. calculated at the main pivot point between the seat bottom and the base) were applied to the actuator mounting holes as well as the seat bottom pivot holes. A minimum factor of safety was calculated as 1.77 around the weld of the main pivot post.
Analysis was not performed on the different links of the linkage system as they only serve to hold the backrest of the seat vertical throughout the tilting range of the seat. Because of this, the only load they will see is due to the weight of the seat back and any force the rider exerts on the backrest. With 8 links made from 3/16 inch thick steel flat bar, they will have no problem supporting this loading.
The safety harness used is a 2 inch lap belt connected to a 2 way anti-submarine belt to fully support the rider’s weight. During the final assembly, the seat was painted and the actuator was connected to wires spliced into one of the cart’s two 12 volt batteries.
Front Axle Design
Three main design options were proposed in order to add stability to the front axle system: to install a wider front tire and otherwise keep the three wheeled design of the cart, to modify the front axle to accommodate two front wheels, or to add dolly wheels to the front sides while keeping a single wheel in the front. Using a House of Quality, the four wheel design was found to offer the most stability of the three designs while also being the safest, and thus was determined to be the best design.
The new tires for the four wheel design needed to be small in order to avoid overloading the cart’s drive motor. They also needed to be fairly wide to increase ground contact area and include a tread for enhanced off road traction. The tires ultimately selected were Carlisle Turf Saver® 9x3.5-4 tires rated at 260 lbs. per tire. A contact area comparison was calculated to compare the ground contact areas of the new tires with that of the original cart tires. The cart originally used three Cheng Shin brand tires 8 inches in diameter and 2 inches wide. Contact area was found to increase increased by 40% for the entire cart.
To determine the maximum stress on the new wheel spindles, it was first recognized that there are two main forces that act on them. One of these is a vertical force generated by the weight of the cart and rider and distributed among the four wheels. The other is a force in the spindle’s axial direction caused by friction at the tires’ contact patch when turning. To determine the vertical force acting on the spindle, the weight of the cart and rider together was assumed to be 350 pounds. Then, to account for uneven weight distribution that could be encountered on hilly terrain, it was assumed that 75% of this weight would act through one wheel in a worst case scenario. This resulted in a normal force from the ground of 262.5 pounds. The calculation of the turning force was slightly more involved. Since the actual turning force is dependent on the coefficient of friction between the tires and the ground, it would be very difficult to calculate because of the wide variance of friction coefficients that could be encountered in off road terrain. Therefore, the force was derived by calculating the maximum centrifugal force experienced by the cart when turning at maximum speed at the tightest possible turning radius. The centrifugal force calculated using this method was 137 pounds. Then, once again due to possibilities of uneven weight distribution, it was assumed that 75% of this force acted through one wheel. By doing this, a turning force of 103 pounds was calculated.
Three dimensional spindle models were then created on which FEA analysis was performed. Two cases were studied, one to simulate the non-turning (only the maximum normal force applied) and another for the turning (both the maximum normal force and turning force applied) conditions. Because of the opposing direction of the bending moments generated by each force, it was determined that the most stressed case for the spindles was when the cart was not turning. The material for the spindles was assumed to be AISI 1020 cold drawn steel. In each analysis, the inside of the pivot tube of the spindle was constrained as fixed geometry and the loads were remotely applied to the face against which the wheel mounts from the location of the tire’s contact patch. From the FEA results, a maximum stress of 3,456 psi and factor of safety of 14.7 was calculated for the turning simulation and for the non turning simulation the maximum stress was 22,000 psi, resulting in a factor of safety of 2.3. Hand calculations were also performed for each case by finding the Von Mises stress at the point where the spindle bolt is welded to its pivot tube. This stress was computed based on the calculated axial, bending, and shear stresses acting at this point. The results showed a maximum stress of 3,238 psi and a factor of safety of 15.44 for the turning case and a maximum stress of 19,800 psi with a factor of safety of 2.525 for the non turning case. Percent differences between hand calculations and FEA analysis were 6.3% for the turning scenario and 10% for the non turning scenario.
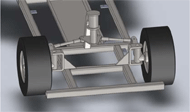
A three-dimensional model of the frame of the existing cart was then created using SolidWorks. The models of the tires, wheels and spindles were then positioned into an assembly with the frame based on desired track width, wheelbase, ride height, and clearance requirements. Once placed, the various components were moved through their range of motion within the model to check for any possible clearance issues. Figure 5 shows the frame of the cart and the final placement of the two front wheels.
The steering system was then added to the model. The steering system includes a simple triangular shaped bracket on the steering column to which the tie rods attach. The tie rods connect this piece to the spindles and allow the cart to steer. The tie rod attachment bracket was designed to provide a motion ratio such that the wheels could sweep their entire range of motion without having to turn the handlebars too far. The attachment bracket was positioned such that it would not cause binding in the tie rod ends at any point in its range of motion. The length of each tie rod was determined from the 3D model.
RESULTS/EVALUATION
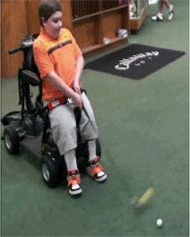
A mobility cart, an Invacare Lynx-L3, was modified to allow a young boy using a wheelchair to play golf, accessing all areas of the golf course with independence. The adapted golf cart allows its user to efficiently maneuver about a golf course and to golf while remaining seated. Figure 6 depicts the “client” using the cart.
The Quebec User Evaluation of Satisfaction with Assistive Technology (QUEST 2.0) tool was used as an outcome measurement instrument to measure satisfaction with the unit [5]. The QUEST items that were assessed include comfort, simplicity of use, effectiveness, ease in adjusting and safety. Each item was scored with a 5-point satisfaction scale ranging from a score of 1 denoting “not satisfied at all” to a 5 indicating “very satisfied”, The “client” was very satisfied with the adapted golf cart.
CONCLUSION
An electric golf cart was developed to allow a young boy with physical impairments to golf independently. The cart is kept at the Crosswinds Golf Club in Perrysburg, Ohio because it has a youth program in which several children with physical disabilities are involved. The cart is thus available to any child with physical impairments to use. Therefore the golf cart will have a positive impact on the lives of many children.
REFERENCES
- Lynx L-3. Retrieved April 17, 2011, from http://www.invacare.com/cgi- bin/imhqprd/inv_catalog/prod_cat_detail.jsp?s=0&prod ID=L-3R&catOID=-536885289
- Sport Rider Electric Scooter by EV Rider. Electric Scooters and Accessories | Medical Mobilizers and Mobility Scooters Distributors | Battery Operated Vehicles and Scooters. Retrieved April 17, 2011, from http://www.evrider.com/sport-rider-electric- scooter.html
- Single Rider Golf Car. Golf Express. Retrieved April 17, 2011, from http://www.golfxpress.com
- The Solo Rider 3400. Solo Rider. Retrieved April 17, 2011, from http://solorider.com/Features.html
- Demers, L., Weiss-Lambrou, R., & Ska, B. (2002). The Quebec User Evaluation of Satisfaction with Assistive Technology (QUEST 2.0): An Overview and Recent Progresses. Technology and Disability, 14, 101-105.
ACKNOWLEDGEMENTS
This work was supported by grant BCS-0931643 from the Research to Aid Persons with Disabilities Program from the Biomedical En. and Eng. Healthcare cluster of the CBET division of the NSF.