Analytical and Empirical Static and Dynamic Stability Testing of a Variable Position Mid Wheel Drive Power Wheelchair
John K. Layer, University of Evansville; Richard Nelson, Criterion Health, Inc. & Easter Seals Rehabilitation Center; Robert M. Levy, Criterion Health, Inc
BACKGROUND
Power wheelchairs (PWCs) are either rear, mid or front wheel drive. Each drive wheel position has its advantages and disadvantages, especially as a function of the terrain and environment. There are currently no power wheelchairs available that can provide the advantages and avoid the disadvantages of a single position drive system.
As a Phase II SBIR project, funded through NIDRR, Criterion Health designed and fabricated a prototype variable position mid-wheel drive system power wheelchair, Varpo (Variable Position). The design was consistent with available popular mid-wheel drive (MWD) power wheelchairs although the wheelbase was approximately 5 cm. longer. The gearboxes, motors, and control system (MK6i) from an Invacare TDX SP power wheelchair base were used.
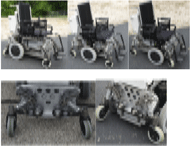
An electromechanical linear motion system was designed and used to change the drive wheel position, and to raise and lower the front and rear casters when in front wheel drive (FWD) and rear wheel drive (RWD) respectively. The rear suspension was manually stiffened or softened for the front and mid wheel drive respectively. The first three panels in Figure 1 show Varpo in Rear Wheel, Mid Wheel, and Front Wheel drive positions with the rear casters raised in rear wheel drive and the front casters raised in front wheel drive. The last two panels in Figure 1 show the rear suspension “soft” for mid wheel drive and “stiff” for front wheel drive.
Prior to conducting testing with end-users, analytical and empirical determination of the static and dynamic stability of Varpo was conducted based on the RESNA/ANSI wheelchair standards. The methods and results of these tests are the focus of this paper.
ANALYTICAL DETERMINATIONS OF STATIC AND DYNAMIC STABILITY
The analytical static and dynamic analysis was conducted with the following assumptions:
-
The Varpo calculated weight was determined to be 360 lbf, without a human operator or test dummy.
-
The 100kg (220.45 lbf) test dummy torso, thighs, and lower leg specifications as defined in the RESNA WC- 11, were used to determine the combined Varpo and test dummy center of gravity, as well as the subsequent static and dynamic stability analysis.
-
The analysis was conducted for the forward speed of 4.5 mph. One rearward speed of 3 mph was also included. The analysis was conducted with three deceleration times: 1 second, 1.82 second, and 2 seconds.
-
Static and dynamic stability analysis was conducted in consideration of incline and decline angles of 0, 3, 6, and 10 degrees as specified in the RESNA/ANSI WC- 11 and WC-22. No lateral stability or turning stability was evaluated in this report.
A “sense of instability” for the purposes of this paper is defined as when the static or dynamic forces experienced by the wheel chair operation tends to rotate or “tip” the wheel chair about the drive wheels or casters in the applicable position, thereby relying on the action of the corresponding tipping casters to absorb some contribution of load.
The analytically determined static stability critical angles associated with the composite Varpo design and 100 kg (220.45 lbf) test dummy was determined to be a 15.68 degree decline (Front Wheel Drive) and 20.40 degree incline (Rear Wheel Drive).
Two predominant dynamic stability configurations of drive wheel position and incline/decline angles is summarized. The first dynamic configuration was the Front Wheel drive position decelerating while moving forward down a decline. Three specific decelerating rates were evaluated with respect to a deceleration rate required to sense instability which was determined from the specific Varpo center of gravity and physical dimensions. Table 1 provides the analytical results of this analysis.
Decel Rate/ Stopping Dist. @ 2 seconds |
Decel Rate/ Stopping Dist. @ 1.82 second |
Decel Rate/ Stopping Dist. @ 1 second |
Decel Rate Required to sense instability |
Sense of Instability Anticipated |
|
---|---|---|---|---|---|
4.5 mph Forward Motion @ 3 Deg. Decline |
3.3 ft/sec2 6.6 ft |
3.6 ft/sec2 6.0 ft |
6.6 ft/sec2 3.3 ft |
7.34 ft/sec2 | No |
4.5 mph Forward Motion @ 6 Deg. Decline |
3.3 ft/sec2 6.6 ft |
3.6 ft/sec2 6.0 ft |
6.6 ft/sec2 3.3 ft |
5.62 ft/sec2 | Yes @ 1 sec. Decel Time |
4.5 mph Forward Motion @ 10 Deg. Decline | 3.3 ft/sec2 6.6 ft | 3.6 ft/sec2 6.0 ft | 6.6 ft/sec2 3.3 ft | 3.31 ft/sec2 | Yes @ 1, 1.82, & 2 sec. Decel Time |
The Front Wheel Drive position configuration was determined to experience a sense of instability at 6 and 10 degree declines during the deceleration from the forward speed of 4.5 mph for the 1.0 deceleration time period. A sense of instability will also be experienced at the 10 degree decline for a 1.82 and 2.0 second deceleration time periods.
The Front Wheel Drive position configuration oriented at a 10 degree decline is very sensitive to decelerations from forward speeds since a very short moment arm exists from the composite center of gravity and the drive wheel. The maximum forward speed would need to be limited to less than 4.5 mph in order that no sense of instability would be anticipated at the 10 degree decline with a stopping distance of 6.0 ft.
The second dynamic configuration was the Rear Wheel drive position decelerating while moving rearward down an incline. Table 2 presents the data from this evaluation.
Decel Rate/ Stopping Dist. @ 2 seconds |
Decel Rate/ Stopping Dist. @ 1.82 second |
Decel Rate/ Stopping Dist. @ 1 second |
Decel Rate Required to sense instability |
Sense of Instability Anticipated |
|
---|---|---|---|---|---|
3 mph Rearward Motion @ 3 Deg. Incline |
2.2 ft/sec2 4.4 ft |
2.4 ft/sec2 4.0 ft |
4.4 ft/sec2 2.2 ft |
10.27 ft/sec2 | No |
3 mph Rearward Motion @ 6 Deg. Incline |
2.2 ft/sec2 4.4 ft | 2.4 ft/sec2 4.0 ft | 4.4 ft/sec2 2.2 ft | 8.54 ft/sec2 | No |
3 mph Rearward Motion @ 10 Deg. Incline |
2.2 ft/sec2 4.4 ft | 2.4 ft/sec2 4.0 ft | 4.4 ft/sec2 2.2 ft | 6.20 ft/sec2 | No |
The Rear Wheel Drive position configuration is dynamically stable at the 3, 6, and 10 degree incline (from the horizontal axis) at 3 mph rearward motion. A sense of instability is anticipated at a maximum angle of a 13 degree incline with a 1.0 second deceleration time period. The rear tipping casters are anticipated to be utilized at the 13 degree incline orientation when decelerating from a 3 mph rearward motion.
EMPIRICAL DETERMINATIONS OF STATIC AND DYNAMIC STABILITY
Empirical static stability testing was conducted using an angle adjustable surface set up as specified in the RESNA/ANSI WC-1 and WC-2 standards. The Varpo prototype was tested for forward tipping facing down a decline, rearward tipping facing up an incline, and lateral tipping facing across an incline. The tipping angle was determined when a sheet of paper could be pulled from beneath the uphill drive wheel or caster of the Varpo prototype. The angle was measured using a digital level with an accuracy of 0.1 degree.
The Varpo prototype was tested with 50 kg, 75 kg, and 100 kg test dummies, and in all three drive wheel positions (FWD, MWD, RWD). Table 3 presents the data from this testing.
Task | Drive wheel position |
50 kg test dummy | 75 kg test dummy |
100 kg test dummy |
---|---|---|---|---|
Tipping angle in degrees | ||||
Rearward tipping facing up the incline | Rear | 16.4 | 15.7 | 15.0 |
Mid | 44.9 | 41.0 | 36.3 | |
Front | 62.5 | 58.2 | 41.4 | |
Forward tipping facing down incline | Rear | 53.0 | 49.4 | 46.0 |
Mid | 49.1 | 46.5 | 44.6 | |
Front | 18.6 | 17.3 | 15.8 | |
Lateral tipping |
Rear | 35.9 | 32.7 | 30.2 |
Mid | 32.8 | 29.0 | 27.3 | |
Front | 35.0 | 32.0 | 29.2 |
The major results were that for FWD facing down the incline and for RWD facing up the incline, the tipping angles were substantially less than for all other conditions. This is due to a system center of mass (weight distribution) location that is static and not optimized for some drive wheel positions and conditions.
Empirical dynamic stability testing was conducted using a commercially available adjustable ramp surface that was 30 feet long and could be set at angles of 0, 3, 6, and 10 degrees as specified in the RESNA/ANSI WC-1 and WC-2 standards. The Varpo prototype was tested for forward tipping while moving forward down a declined surface, and for rearward tipping while moving in reverse down a declined surface. Each test was performed with 50 kg, 75 kg, and 100 kg test dummies and at wheelchair controller braking (deceleration rate) set at 50%, 75%, and 100% of maximum. Braking was initiated by three methods as specified in the RESNA/ANSI WC-1 and WC-2 standards (let go of the joystick, turn off the power switch to the joystick, and move the joystick quickly in the opposite direction of travel). In order to maintain directional control of Varpo and reach true full speed during the test the left turn and right turn joystick quadrants were turned off so that Varpo would only move straight in forward or reverse.
The testing consisted of reaching full speed on the testing surface and then initiating braking (deceleration) by each of the three methods. The dynamic test results were observed and scored using a scale specified in the RESNA/ANSI WC-1 and WC-2 standards. Table 4 presents the scoring scale.
Condition |
Observed Dynamic Response |
Score |
No Tip |
At least three wheels remain on the test plane at all times. |
3 |
Transient Tip |
Less than three wheels remain on the test plane at some point during the test and then drop back onto the test plane, whether or not any anti-tip devices contact the test plane. |
2 |
Stuck On Anti-Tip Device |
The wheelchair anti-tip devices contact the test plane, and the wheelchair remains stuck on the anti- tip devices. |
1 |
Full Tip |
The wheelchair tips completely over (90 degrees or more from its original orientation). |
0 |
A “sense of instability” for the purposes of this paper is defined as when the static or dynamic forces experienced by the wheelchair operation tends to rotate or “tip” the wheelchair about the drive wheels or casters in the applicable position. A score of 3 indicates a stable condition, with no “sense of instability” perceived by the wheelchair operation. A score of less than 3 indicates a physical tipping condition, and a “sense of instability” perceived.
Due to the observed severity of some of the scores of 2 and zero on the 3 and 6 degree decline surfaces during the empirical dynamic stability testing, it was decided not to test the Varpo prototype on the 10 degree decline surface until a later time.
The 50% braking setting has a stopping time of approximately 2.35 seconds, 75% is approximately 1.75 seconds, and 100% is approximately 1.20 seconds.
The RESNA/ANSI WC-1 and WC-2 standards specify dynamic testing with the wheelchair controller set at 100% forward and reverse speeds. The forward speed on level surface for dynamic stability testing was approximately 5.8 mph, and the reverse speed was approximately 6.2 mph.
Forward Tipping Results
In the RWD and MWD configurations the scores for all testing conditions were a value of 3. In the FWD configuration the first score of 2 (transient tip) was observed with a 50 kg dummy, 50% deceleration rate, 6 degree decline angle, by reversing the joystick position for braking. This transient tip was considered mild as the rear casters only raised off of the ground approximately 1”. All transient tips at 50% braking, on the 6 degree decline with all dummy weights, were observed to be mild. As the deceleration rate increased to 75% and 100%, transient tips were observed on all decline angles (0, 3, 6 degree) and the severity (distance the rear casters raised off the ground before dropping back down) increased as the decline angle and deceleration rate increased. No scores of 1 or zero were observed in the FWD configuration for forward tipping.
With the current Varpo prototype, when moving down a decline of up to 6 degrees in the FWD configuration at a top speed of 5.8 mph, the braking must be set at no more than 50% (2.35 second stop time) in order to remain in a safe dynamic condition. The default manufacturer settings for braking for the Invacare MK6i control system used for the Varpo prototype range from 30% to a maximum of 50%.
Rearward Tipping Results
In the FWD and MWD configurations the scores for all testing conditions were a value of 3. In the RWD configuration the first 2 was scored with a 50K dummy, 50% deceleration rate, 6 degree decline angle, with all three braking methods. As the deceleration rate remained at 50% on the 6 degree decline and the dummy weight increased to 100 kg, the first zeros were scored (full tip over) when releasing the joystick and when reversing the joystick position. With a decline angle of 3 degrees, a dummy weight of 100 kg and a 75% deceleration rate, zeros were scored when releasing the joystick and reversing the joystick position. At 100% deceleration rate zeros were scored on the 3 degree decline with all dummy weights when releasing the joystick and reversing the joystick position. No scores of 1 or zero were observed on the 0 degree (level) testing surface.
With the current Varpo prototype, when moving down a decline of up to 6 degrees in the RWD configuration at a top speed of 6.2 mph, the braking must be set at less than 50% (2.35 second stop time) in order to remain in a safe dynamic condition. The default manufacturer setting for reverse speed on the Invacare MK6i control system used for the Varpo prototype is typically less than 50% (3.03 mph) and the reverse braking is typically less than 40%.
DISCUSSION
Static Tipping Comparison
Analytical and empirical FWD static tipping performance results for the Varpo prototype with a 100 kg test dummy are similar. Analytical FWD tipping angle was calculated to be 15.68 degrees, and the measured empirical tipping angle was 15.8 degrees.
Analytical and empirical RWD static tipping performance results with a 100 kg test dummy are slightly different. Analytical tipping angle was calculated to be 20.40 degrees, and the measured empirical tipping angle was 15.0 degrees. The analytical calculations were based on the center of mass (COM) of the final 3D Varpo model before construction. After construction of Varpo, the controller for the linear motion system was moved rearward approximately 3 inches. This shifted the COM rearward, which decreased the empirically measured static tipping angle in the RWD configuration drastically, while only slightly affecting the FWD tipping comparison.
Dynamic Tipping Comparison
The Varpo prototype was initially set up with a standard Invacare MK6i controller that was not equipped with the optional G-Trac gyroscope system. The maximum forward speed without the G-Trac system is 4.5 mph, which was the speed used for the analytical dynamic stability calculations for this project. The maximum forward speed with the G-Trac system is 5.8 mph, and the maximum reverse speed is 6.2 mph. The G-Trac system was provided and installed on the MK6i controller after the analytical calculations were performed, and before the empirical testing occurred. During the empirical testing the forward speed was 5.8 mph, and the reverse speed was 6.2 mph. The RESNA/ANSI standards specify that the control system for the wheelchair must be set at the maximum forward and reverse speeds for all testing.
The analytical dynamic performance of Varpo in the FWD configuration with the 100 kg test dummy during the 0, 3, 6, and 10 degree decline ANSI/RESNA WC-2 testing was that a sense of instability will not be experienced during 1.82 second deceleration time period (6 ft. stopping distance) from a speed of 4.5 mph, except when decelerating on a 10 degree decline. A less than 4.5 mph forward speed limit operating with a deceleration stopping distance of 6 ft. may be advisable during the FWD position operation on a 10 degree decline.
During empirical testing in the FWD configuration the first score of 2 (transient tip) was observed on a 6 degree decline at 5.8 mph, with a 50% (2.35 second stopping time) deceleration setting. This was a mild transient tip. As the deceleration rate was increased to 75% and 100% the tipping conditions became much more severe and unsafe. This supports the analytical conclusion that forward speed and deceleration rate in FWD are critical and must be set at safe levels.
The analytical dynamic performance of Varpo in the RWD configuration with the 100 kg test dummy is stable at the 0, 3, 6, and 10 degree decline (from the horizontal axis) at 3 mph rearward motion. A sense of instability is anticipated at a maximum 13 degree decline with a 1.0 second deceleration time period. The rear tipping casters are anticipated to be utilized at the 13 degree decline orientation when decelerating from a 3 mph rearward motion.
During empirical testing in the RWD configuration the first score of 2 (transient tip) was observed on a 6 degree decline at 6.2 mph with a 50 kg test dummy, with the deceleration rate set at 50% (2.35 second stopping time). As all wheelchair settings remained the same and the dummy weight was increased to 100 kg the first score of zero (complete tip over) was observed. This supports the analytical conclusion that speed in the RWD configuration must be limited to 3 mph, and that deceleration rate must be set at safe levels.
CONCLUSIONS
In general the analytic and empirical analyses of static and dynamic stability of the Varpo prototype were consistent. They identified significant design and performance challenges that will need to be addressed with the Varpo prototype when going in the forward direction down a decline in the FWD configuration, and when going in the reverse direction down a decline in the RWD configuration.
The RESNA/ANSI WC-1 and WC-2 standards specify that speed and deceleration rate must be set at 100% for all testing. It has been found that with the Varpo prototype, in the FWD configuration, 75% and 100% deceleration rates are very unsafe when moving forward down a declined surface. It has been found that, in the RWD configuration, a 100% speed setting of 6.2 mph is very unsafe when moving in reverse down a declined surface.
REFERENCES
[1] RESNA American National Standards for Wheelchairs WC-1: 2009, Volume 1: Requirements and Test Methods for Wheelchairs (including Scooters).
[2] RESNA American National Standards for Wheelchairs WC-2: 2009, Volume 2: Additional Requirements for Wheelchairs (including Scooters) with Electrical Systems.
ACKNOWLEDGEMENTS
Supported by NIDRR grants (H133S100082 and H133S090013) and Indiana 21st Century matching funds.