The Finite Element Analysis Of Pressures Inside The Body While Lying Down On Mattress
Shigekazu Ishihara, Keiko Ishihara, Mitsuo Nagamachi*
Department of Rehabilitation Engineering, Hiroshima International University, Higashi-Hiroshima, Japan
*International Institute of Kansei Design, Kure, Japan
ABSTRACT
Preventing bedsore is one of the common problems between many disciplines related with paralysis. We have developed a bedsore preventive mattress and a wheel chair cushion. Through the development, we have numerous body pressure measurements on different mattresses and cushions. Such measurements require long time and lots of efforts. Thus, simulation of body pressure has a potential to estimating pressure distribution that caused by physical parameters of different mattresses. In this study, we show attempts to modeling of body and estimate the pressure on its transverse plane. Its computation was based on non-linear finite element method of hyperelastic materials such as muscle, skin and fat. Since it simulates different tissues, we could estimate the pressure not only surface, also pressure inside the trunk. The simulated results are well accorded with actual pressure measurement results.
BACKGROUND
The bedsore is a quite common problem between rehabilitation, care and gerontology. Unrelieved pressure, friction, humidity, shearing forces, temperature, and under-nourishment are main causes of the bedsore. Restricted blood flow fails reconstruction of skin tissue. Lots of patients suffer it, especially, half body-paralyzed person by brain infarction are significant. Causes and measures are shown in below.
- Pressure: reducing body pressure, and decentralizing weight
- Friction: Soft touch
- High Humidity: Ventilation
- Poor nutrition: Nutrition control
- Inhibited blood flow: Highly rebounding material for assisting easy self-movement (tossing)
Numerical analysis of stress and strain conditions becomes popular in the design process of metal parts, architectures, constructions and surgery. Most of them are analyzed with Finite Element Method.
Haex (2005) analyzed displacement of spine and mattress at side lying position. The body has modeled by head, shoulder, chest, pelvis and feet. Stress and strain of mattress are caused by weight of each part of the body.
THUMS developed by TOYOTA central R&D laboratory is the virtual human body model that has both bone and organs. It is very expensive and made for extreme external force, because it was developed for collision simulation.
Yoshida et al. (2008) developed their own body model to research sleeping comfort. Bones, ligaments, intervertebral disk are assigned as linear elastic materials, and softer tissues like fat, muscles are assigned as hyperelastic materials. Interactions between the body and the mattress are analyzed at sagittal plane.
We developed a bedsore-preventing mattress with joint research between Panasonic, Toyobo and Wadatestu Co.Ltd. Breath Air, the material developed by Toyobo has excellent pressure diffusion and durability. It does not absorb water and could be dry quickly. With these properties, it is potentially good material for bedsore preventing mattress. The aim of development was achieving better pressure dispersion than high-density urethane and comfortable sleep. At the first step, we measured body pressure on the BreathAir those have different density and thickness. Then, we chose candidates and made them as double layer samples to adapting a large range of body weights.
The finest candidate has two layers, softer fiber layer and hard fiber layer of BreathAir. Body pressure dispersion is better than HD urethane, and subjective comfort evaluation is also best. The product, LuckMatAir was launched in December 2008 from Panasonic, and it got success quickly (Nagamachi et al, 2010, Ishihara et al., 2010, Panasonic web page, 2008).
Through this research and our other research on the conventional bed mattress, we have made many measurements of body pressure and deflections. These measurements take lots of efforts and costs. Seven months of measurement are required for the development of LuckMat Air.
We got an idea of physical simulation, since stress and strain of the material are the physical phenomenon. Computer simulation also gives benefits. Physical parameters such as elasticity could be varied in simulation without making costly prototypes. Displacements and pressure distribution inside the body could be modeled.
PURPOSE
The purpose of this study is to develop the finite-element model of human body and make confirmations with actual pressure measurement. It will contribute to effective development of the mattress. Furthermore, it will give simulation and visualization of both strain inside the body and interactions with mattress.
At first, we made simple body truncal model and then made simulation of displacement and stress. After that, we compared with pressure measurement on the real mattress, to validate the computer model.
METHOD
Finite element model of human body
Sizes for Japanese people are referenced with AIST database (AIST, 1992). In this simulation, we used the width of iliac crest, abdominal depth, shoulder breadth and diameter of arm base. FEM modeling and computation were done with ANSYS 12 (ANSYS.Inc., www.ansys.com ). We referred anatomical and MRI images from The Visible Human Project, for making the shape of cross-section of the body.
Average measure of Japanese male (mm) |
|
Width of iliac crest |
250 |
Abdominal depth |
132 |
Shoulder breadth |
456.2 |
Arm joint diameter |
126.3 |
Our model has seven substances; skin, subcutaneous fat, muscles, visceral fat, bones, esophagus and trachea. Skin, fat and muscles are soft tissues. They are modeled as non-linear hyperelastic materials, by Ogden’s formulation. Bones are modeled as non-linear elastic material. Esophagus and trachea are modeled as non-linear elastic materials.
Non-linear hyperelastic material has a property like soft gum. It deforms by small force, and its deformation is out of proportion to the force. For example, the first force makes first deformation. Then, the second force was three times larger than the first force, its deformation was smaller than three times of first deformation. When it has “large deformation” (larger than 1 deformation), it will deform plastically without fracturing or breaking. Usually, elastic material will break with smaller force than hyperelastic material.
Material constants
Stress and strain analysis by FEM requires material constants. Young’s modulus and Poisson’s ratio. Young’s modulus shows the stress and strain relation. Poisson’s ratio shows the negative ratio of transverse to axial strain. When the material is incompressible (volume does not change) and deforms elastically, its Poisson’s ratio becomes 0.5. If it is compressible (i.e. Cork) and not changes its transversal size, it is near 0. Most of the solid materials have values between 0 to 0.5.
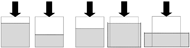
Material constants used in this analysis are shown in below table. Parameters of human tissues are referenced from Linder-Ganz & Gefen (2004) and Yamamoto et al. (2008). HD urethane parameters are referenced from the home page of Fuji Gomu Ltd. (http://www.fujigomu.co.jp/simulation/urethan/)
We used Ogden’s formulation for hyperelastic materials’ stress and strain model. Strain energy W is defined as formula in eq.(1). N is positive constant, each λ is extension ratio on each axis, and α and μ are material parameters.
(1)
Hyperelastic materials | μ (MPa) | α | Density (kg/m3) |
fat | 0.01 | 30 | 1200 |
mascle | 0.003 | 5 | 1056 |
skin | 0.008 | 10 | 1056 |
Elastic materials | Young’s modulus | Poisson’s Ratio | Density (kg/m3) |
bone | 2×104 | 0.3 | 800 |
esophagus and trachea | 0.047 | 0.49 | 1056 |
HD urethane | 0.025 | 0.0 | 48 |
Contact Analysis
In this research, we made a contact analysis between mattress and trunk. To analyze stress and strain with the contact, we must set the contact point and friction. Without setting touching point, the body slightly slips on the mattress, when add the gravity to the model. Inside of the body, bone, muscles and fat have disintegrated because each material has different deformation. We referred the page of Prof. Klamecski of Minnesota University, for setting contacts and analysis.
Lumbar modeling
We made two-dimensional cross-section (transverse section) lumbar model. Shape and position of tissues are taken from images of the Visible Human Project. Width of iliac crest is 250mm, which is Japanese male average. Trunk model and mattress have decomposed (meshed) to triangular elements. Five different materials have assigned; skin, fat, muscle, bone and mattress. Mattress has 50cm width and 9cm thickness.
For contact analysis, contact points are defined between the trunk and the mattress. Friction coefficient is 0.5. Undersurface of the mattress was fixed. Stress and strain of mattress, lumbar, and inside of the lumbar was computed. Every material in the simulation has own weight by acceleration of gravity (9.8m/s2).
Upper shoulder modeling
The size of the shoulder model was assigned also average Japanese male size. Shoulder breadth is 45.62cm and arm joint diameter is 12.63cm. This time its mesh is tetragon.
RESULTS
Lumbar simulation
When we simulated 60kg male body, maximum stress on the skin was 39mmHg, stress on the subcutaneous fat was 19mmHg, when lying down on the mattress which Young’s modulus was 25 kPa. The mattress was slightly strained by body weight.
Comparison with actual pressure measurement (lamber)
We have compared the simulation result with actual measurement of body pressure. Pressure distribution was measured with FSA system (Force Sensitive Applications, Canada). Commercially produced high-density urethane mattress was used. The subject was 71 years-old male and his weight was 63kg. We asked the subject to lying down on mattress, and measured pressure on the mattress for 10 minutes. The subject wears tracksuit bottoms and thin polo shirt.
Averaged measured pressure around the sacrum was 32.03mmHg. Simulated pressure of correspondent area was 31.26mmHg. The difference was small, thus, we think this FEM simulation has good proximity.
Upper shoulder simulation and comparison
This time we also set 60kg male body for simulation. The maximum pressure on the skin was 19mmHg and 28.7mmHg on subcutaneous fat. Estimated pressure was smaller than lumbar, because the upper shoulder has large and thick muscles around the bones.
Averaged measured pressure of the corresponding region has 9.87mmHg. The simulation result was 8.43mmHg. The difference is 1.4mmHg and it was regarded as a small value.
CONCLUSION
We have shown attempts to modeling of body and estimate the pressure on its transverse plane. Its computation was based on non-linear finite element method of hyperelastic materials such as muscle, skin and fat. Since it simulates different tissues, we could estimate the pressure not only surface, also pressure inside the trunk. The simulated results are well accorded with actual pressure measurement results. We are now testing with different mattress and also with different body types.
REFERENCES
Haex, B., (2005). Back and Bed – Ergonomic aspects of sleeping, CRC press.
Toyota motors (2012). THUMS, Retrieved from http://www.toyota-global.com/innovation/safety_technology/safety_measurements/thums.html.
Yoshida, H. (2008). FEA on comfort sleep of bed mattress, 10th Proc. of Japanese Kansei Engineering Society conference (in Japanese) (CD-ROM).
Nagamachi, M., Ishihara, S., Nakamura, M. and Morishima, K. (2010). Kansei Engineering Development for a Preventing Bed Sore, Gerontechnology, 9(2), 312.
Ishihara, S., Nagamachi,M., Nakamura,M. and Morishima, K. (2010). Development of a wheel chair cushion with Kansei ergonomics, Gerontechnology, 9(2), 222.
Panasonic (2008), LuckMat Air, Retrieved from http://panasonic.biz/healthcare/afsh/products/home/bed/slim/
National Institute of Advanced Industrial Science and Technology (1992), AIST Japanese human size database 1991-92, Retrieved from http://riodb.ibase.aist.go.jp/dhbodydb/91-92/
The Visible Human Project (2003), Retrieved from http://www.nlm.nih.gov/research/visible/visible_human.html
Ogden, R. W., (1972). Large Deformation Isotropic Elasticity - On the Correlation of Theory and Experiment for Incompressible Rubberlike Solids, Proceedings of the Royal Society of London. Series A, Mathematical and Physical Sciences, 326(1567),565-584.
E. Linder-Ganz, E. and Gefen, A. (2004), Mechanical compression induced pressure sores in rat hindlimb, muscle stiffness, histology, and computational models, Journal of Applied Physiology, 96, 2034-2049.
Yamamoto, Y. et al. (2008), Biomechanical simulation for prevention of pressure ulcers (1. FEM simulation), Seitai-ikougaku, 46(5), 489-494 (in Japanese).
Klamecki, B. E. (2009), Use of ANSYS 10.0 for Contact Analysis with Hyperelastic Material, Retrieved from http://www.menet.umn.edu/~klamecki/index.html