- Federal Technological University of Paraná. Avenida dos Pioneiros, 3131 CEP 86036-370, Londrina, Brazil, +55 (43) 3315-6100 - Fax +55 (43) 3315-6121, genaro@utfpr.edu.
- Wadas T. MSc Automotive Engineering, Birmingham City University, Birmingham, UK, tatiwadas@gmail.com
Abstract
This article describes the development of a motorized off-road wheelchair, consisting of two parts; first part corresponds to the wheelchair and the second one to the traction system that is coupled to the wheelchair which makes it a three-wheeler, thus allowing quick and safe movement for wheelchair user. For the development of the prototype wheelchair, processes akin to standards, knowledge, experience and regulations previously used to develop vehicles called BAJA and Energy Efficiency, were used.
INTRODUCTION
The following work shows the development of a prototype intended for people with physical disabilities, who lack or have limited functionality in their lower limbs, for example, people who find themselves in a position to require the use of a wheelchair. The prototype of the off-road wheelchair has manual and electric propulsion for use on variable terrain, like on trails and rural roads, allowing for rapid and safe mobility in order to provide the freedom to travel short or long distances, and still being capable of being used in sports practice.
The most widespread wheelchairs on the market were designed for temporary use, ranging from hours or days, however in many cases they are used as permanent mobility solution, causing discomfort and diseases to the wheelchair user, as well as to those who help the wheelchair users.
The shape of the proposed vehicle is a tricycle, i.e., a vehicle with three wheels, two that are part of the chair and a third septate wheel, which will be used for braking, transmission system and steering. These conventional vehicles are made in order to prevent its rolling (the rotation of the vehicle around the X axis) and do not allow dynamic changes in camber angle (tilting).
Thus, this kind of vehicle is stable and it can be driven in a similar manner to a car. However, as every vehicle can present risk behaviours (tipping and roll) due to reduced area of the base of the rider's polygon stability, in the case of a tricycle, the figure generated by the contacts is a triangle. [1]
Tricycles can have two configurations, the delta type and tadpole type. The delta type, has a front wheel and two at the rear; where, the front wheel is responsible for steering. Tadpole has a configuration of two front wheels and one at the rear, allowing the steering system to be positioned on the front wheels or the rear wheel. For the specific case of the wheelchair, a delta and tadpole configuration is chosen, as it can shown in figure 1.
The drag angle is important to the handling, especially in the steering process, and is also responsible for the bike tilt when on curves. The positive angle of drag and the steering angle combine to produce a moment around the steering shaft, that allows the movement of the vehicle in a straight line, thus providing good straight-line stability.
The angle of attack, affects the response-speed of the motorbike, which are given through steering inputs. It can also be asserted that the greater the angle, the greater is the straight-line stability; as the wheel divided over the power that comes from the obstacle and affects the vehicle chassis the least. The classic example of excessive use of this angle for straight-line stability, are the choppers. These vehicles on curves can present the sub-steering phenomenon, and due to this, the race bikes have a small angle.
The wheels of the wheelchair traditionally uses neutral camber (90°) relative to the ground. Negative camber is widely used in sport wheelchairs. The negative camber allows for better stability and ease to go around curves. But the larger the camber, value greater is the value of the energy consumed. [5] Thus, this setting should also be considered in the tadpole tricycle type, whereas the rear wheel will be driven and used for steering.
The delta-type chair, figure 3, presents some difficulties due to the low friction of the front wheel, which decreases the efficiency of the steering, braking and transmission, especially during uphill and on wet paths. This is due to the gravity centre position which is too far behind the pivot. [6]
SUSPENSION
There are several suspension models, each one with its specific characteristics, for the front suspension the most common models are the Dragged Arm, Double A, MacPherson and Multi Link.
Front suspension type Double A
The double Wishbones suspension model, as shown in Figure 4, is the system most often applied in vehicles, it can be used in both the front and rear suspension. It operates independently and is a model which has better relation with the angles required for a good operation of the suspension.
The modelling of suspension travel acts to always keep the wheel perpendicular to the surface of the ground, independent of the action of the springs, the vehicle loading and the body tilt on a curve, thus it ensuring an excellent performance in terms of stability .
Rear suspension with swing arm
The use of the front articulation of the swing-arm as a support and attachment of the rear axle to the rear end of the arm allows the wheel to respond quickly to track surface variations.
The basic configuration of the rear suspension with the swing-arm, can be divided into some categories depending on the number of buffers used and the type of the oscillating arm. In the conventional type, two sets of dampers / springs, supported at the end of the swing-arm support the rear part of the chassis as shown in Figure 5.
PURPOSE
To develop a prototype of a wheelchair off-road, using SAE International Methodology “Baja SAE® Series Rules”[9] and SAE SUPERMILEAGE® RULES”[10]
METHOD
Parameters |
Values |
Rake angle |
10° |
Trail |
10 cm |
Offset |
3 cm |
Negative camber |
6° |
The activities to be performed in the project development should follow a sequence of actions established chronologically. In the stage of conceptual design, the knowledge and experience acquired in baja projects, energy efficiency and accessibility of vehicles will be used, (SAE INTERNATIONAL Regulations “Baja SAE® Series Rules”, “2016[9] SAE SUPERMILEAGE® RULES”[10] bibliography, etc.) and are adapted to contemplate the minimum requirement of ABNT NBR ISO 7176[12]. Wheelchair and the ABNT NBR 9050:2004 Standard[11]: that establishes the technical criteria to be observed during the design, construction, installation and adaptation of buildings, furniture, spaces and urban facilities for accessibility conditions.
1) Static Proof: Project report: present a clear, summarized and organized the engineering information and processes used in the development for each prototype system.
2) Dynamic Proof: Acceleration, Maximum Speed, Braking, Traction (Pull Track). Suspension and Traction, others.
RESULTS
The table 1 shows the front suspension parameters used to develop the prototype.
The wheelchair shows negative camber to give greater stability to the prototype on all terrains.
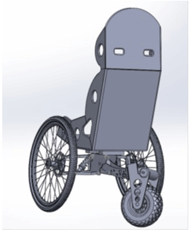
CONCLUSION
The prototype has a simple construction that has it's own mechanisms for rough roads, containing of an independent front suspension and rear suspension PRO-LINK swing arm suspension.
All three wheels will have disc brake systems, for driver safety will use a shell-type seat belt with 5 points safety harness.
The prototype is within the dimensional limits for use accessibility spaces. The equipment can be moved manually by the user or support person and will also have a 1000W electric motor.
REFERENCES
[1] GAUDENZI de Faria M. (2010). Tilt control based on steering for three-wheeler variable camber. Master Dissertation UFSC.
[2] Velomobiles. Retrieved January 18, 2015, from http://velo-city.org/velomobiles/index.html
[3] FOALE, T. Motorcycle Handling and Chassis Design—The Art and Science,Tony Foale Designs, Alicante, Spain (2003). Retrieved January 15, 2015, from http://www. tonyfoale.com
[4] DONADIO, R.N. Modeling of the directional behavior of motorcycles during cornering. / Rafael das Neves Donadio - São Bernardo do Campo (2009). Final Project – University Center da FEI. Supervisor Prof. Dr. Roberto Bortolussi 124f. : il
[5] FAUPIN et al. Wheel camber and wheelchair sprinting Journal of Rehabilitation Research & Development-JRRD, Volume 41, Number 3B (2004) pp421-428s
[6] GILAPA Genaro. Vehicles accessibility development from experiences in baja and supermileage, international workshop on assistive technology (2015).
[7] LAJQI etal, DESIGN OF INDEPENDENT SUSPENSION MECHANISM FOR A TERRAIN VEHICLE WITH FOUR WHEELS DRIVE AND FOUR WHEELS STEERINGANNALS OF FACULTY ENGINEERING HUNEDOARA – International Journal Of Engineering, TomeXI-Fasc 1, ISSN 1584-2665, pp 101 – 108 Retrieved February 8, 2016, from http://annals.fih.upt.ro/pdf-full/2013/ANNALS-2013-1-12.pdf
[8]19. REAR SUSPENSION, MOTO HONDA DA AMAZÔNIA LTDA. System description, After-sales Service Department. Sector of technical publications, p. 19-2
[9] SAE internacional (2016). Collegiate Design Series Baja SAE® Rules. Retrieved February 8, 2016, from https://www.bajasae.net/content/2016_BAJA_Rules_Final-9.8.15.pdf
[10] SAE internacional (2016). SAE SUPERMILEAGE® RULES. Retrieved February 8, 2016, from http://students.sae.org/cds/supermileage/rules/2016supermileage_rules.pdf
[11] THE BRAZILIAN ASSOCIATION OF TECHNICAL STANDARDS. Accessibility to buildings, furniture, urban and equipment spaces [NBR 9050]. Rio de Janeiro: ABNT (2004), p. 97
[12] ISO 7176-3:2003, Wheelchairs — Part 3: Determination of effectiveness of brakes, Second edition (2003) Retrieved January 18, 2015 from www.iso.org
ACKNOWLEDGEMENT
This work was supported by Bruning Tecnometal of Rio Grande do Sul State and to UTFPR - Federal Technological University of Paraná - Campus Londrina.