Ji Chen1 ,2
, Irwin A. Munoz
1
, Diane Damiano
1
, Thomas C. Bulea
1
1
Functional and Applied Biomechanics Section, Clinical Center, National Institutes of Health
2
Biomechanical Engineering Program, Department of Mechanical Engineering, University of District of Columbia
INTRODUCTION
Orthotics are a common treatment option for individuals with cerebral palsy (CP) who have crouch gait which is characterized by excessive knee flexion [ ]. Compared to robotic exoskeletons (or active orthoses), passive (spring or damper based) orthotics can offer smaller form factor and less complexity because no motor, transmission, sensors, electronics, or power supply are needed to provide assistance. Passive orthoses can provide stretching and mobility assistance for walking. Commercially available passive orthoses like Levitation from Springloaded Technology or C-Brace from Ottobuck [ ],are primarily designed to benefit people in the early stages of degenerative diseases such as multiple sclerosis, or in advanced stages of osteoarthritis, as well as those with incomplete paraplegia. These devices focus on improving knee stability and symmetry of movement, reducing knee pain, and enhancing balance and coordination. Passive orthoses are also good candidates for people with crouch gait from CP who may benefit from augmenting their weak extensor muscles when assisting knee extension .
Commercially available passive orthoses for crouch gait deliver extension assistance through two approaches. The first is to assist lower limb extension using a leaf spring design, e.g. as seen in the DAFO 3.5 (Cascade DAFO, Inc., Ferndale, WA); however, the amount and timing of assistance provided is variable. The second approach uses adjustable dynamic response (ADR) technology (Ultraflex, Pottstown, PA) that provides variable resistance to flexion. Both approaches have shown improved stride length, hip extension in stance and dorsiflexion in swing compared with barefoot walking [ ]. Recent work from our group at NIH has shown that robotic exoskeletons can significantly improve walking kinematics by providing knee assistance during stance and late swing phases of walking [ ]. In that study, relatively low torques resulted in significant improvement in knee extension with concurrent engagement of the knee extensor muscles in children with crouch gait from CP. Based on these results, we hypothesized that providing knee extension assistance proportional to knee flexion angle would improve walking performance and engagement of the weak extensor muscles. Further, we hypothesized that such a torque profile could be supplied during stance with a properly designed passive mechanism. To evaluate that hypothesis, we designed two spring-based knee braces and evaluated their torque assistance through simulated walking performed in a Biodex dynamometer. Our approach is to make the knee extension assistance adaptive (proportional or reverse proportional) to knee angle by manipulating the spring stiffness and moment arm of spring. This approach has been previously used by Dr. Chen during his doctoral research to develop passive devices (HandSOME [ ] and SpringWear [ ]) for arm and hand rehabilitation of stroke survivors.
METHODS
We developed two different passive knee mechanisms that can be attached to a knee-ankle-foot orthosis (KAFO) to create a prototype extension assist device (FreeGait). . The primary difference between the two prototypes is the type of spring used. Design 1 employs an elastic-spring whereas Design 2 employs a compression spring.
Design I (Elastic Design)
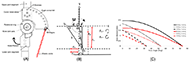
The elastic spring design is shown in Fig.1. A linear elastic spring, composed of multiple cords mounted in parallel between the shank and thigh, provides torque across the knee joint in the sagittal plane. A free hinge joint was used to allow free rotation between the thigh and shank uprights. Assistive torque (M) is a function of
as labeled in Fig.1B. Here κ is the total stiffness of the elastic spring, δ is the distance between knee joint axis and the attachment point of elastic springs on the curved metal piece, x the current length of elastic springs, x0
the resting length of elastic springs, F the generated elastic force. The angles defined here are used to derive the governing equation for torque. The assistance profile can be tailored to specific activities by changing the spring mounting points and stiffness as shown in Fig. 1C. For example, a mounting angle of 90° can be used in walking tasks that need assistance during the knee's full range of motion such as sit-to-stand whereas lower mounting angles (i.e., 40° and 60°) can be used when extension assistance is only necessary at knee angles close to full limb extension such as for stretching or walking tasks. For each mounting angle the magnitude of assistance can be increased or decreased by adjusting spring stiffness.
Design II (Compression Spring)
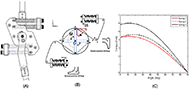
Design II (Fig.2) is an adaptation of a previously designed compression spring mechanism for gravity compensation during gait rehabilitation [ ]. Compression springs have greater stiffness than elastic springs, which can produce higher force at the cost of more weight. In this design, two pairs of compression springs are arranged on opposite sides of the knee rotation axis as shown in Fig. 2A. Each pair of springs are mounted on linear bearings with a pair of stabilizing aluminum blocks on either end. A thin polyester cable (0.042 inch in diameter) is routed between the stabilizing bars to connect the pairs of springs and transfer their force across the knee joint during knee rotation. The cable routing path was designed to provide increased assistance as the knee extends, and reduced assistance at greater knee flexion angles. C-shape spacers were designed and mounted on the linear guide to enable the springs to be pre-tensioned on the knee brace to ensure torque assistance when the knee is at a fully extended position. The force diagram is shown in Fig. 2B and the assistance torque (M) is a function of κ, AO, OF, α, Δ, x0
as labeled in Fig.2B. As the knee extends, the cable (gray line in Fig. 2B) releases the spring tension to increase assistive torque. The amount of assistance can be adjusted by changing spring pretension or spring stiffness; the torque profiles for 3 different stiffnesses (3956 N/m 5301N/m, 5399 N/m respectively are shown in Fig.2C.
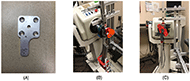
Torque assessment
A Biodex dynamometer (Biodex Medical Systems, New York, NY) was used to simulate knee motion and evaluate the torque profiles provided by the two passive orthosis prototypes. The Biodex was set to passive movement mode with a 90 degree range of motion (full extension at 0 -90◦ knee flexion) at 10◦/s angular velocity. The prototypes were mounted to the Biodex rotation joint through a customized aluminum flange (Fig. 3). A force-torque sensor (JR3 Inc., Woodland, CA) mounted on Biodex collected the overall reaction torque from the devices. To compute the net assistive torque the gravitational and friction torque were measured without springs attached and subtracted from the torque measured with springs attached. A LabView program (National Instruments, Austin, TX) was used to collect the knee angle and joint torque data at 1000Hz sampling rate. A customized filtering algorithm (a 30th-order median filtering followed by a Savitzky-Golay filtering with a 1st order and 17 framelength) was used to smooth the torque data during data processing. The root mean square errors (RMSE) were calculated to examine the agreement between the predicted torque from the design and the torque measured by the Biodex over three trials of simulated flexion and extension with each mechanism.
RESULTS & DISCUSSION
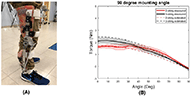
Two prototypes were fabricated and assembled for initial fit testing and assistive torque measurement (Figs. 4 and 5). Both designs are modular and can be attached to standard KAFO uprights. Design 1 weighed 0.4kg and had a frontal plane width of 3.0cm, demonstrating that it could be easily mounted on a KAFO (Fig. 4A). The measured torque profile from Design I followed the prescribed design profile (Fig.4B). Torque RMS with the 2-string configuration was 0.4Nm and the 3-string configuration was 0.2Nm. The weight and frontal plane width of design II was 0.6kg and 6.5 cm respectively, demonstrating that it could be easily mounted on a KAFO as well (Fig. 5A). The measured torque forms for design II is 0.4Nm (Fig. 5B). The estimated torque for Design II reflects the limited capability of the existing prototype to hold pre-tension in the cable. Future improvements for design II include incorporation of a tensioner pulley and fabrication from machined aluminum rather than 3D-printed plastic to increase assistive torque profile.
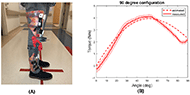
We anticipate Design I may be most appropriate for individuals with mild-moderate crouch gait because assistance is sustained at relatively low levels for knee angles less than 30 degrees. Conversely, Design II, which provides greater assistance and provides maximum assistance at knee angles between 30-50 degrees, can be used for those with moderate to severe crouch. The passive FreeGait has the potential to improve posture and reduce energy cost of walking in individuals with crouch gait from at a more affordable cost than a robotic exoskeleton. It may even help preserve independent mobility in those at risk of losing it – like many adults with CP. However, since it may compensate for weakness and the inability to straighten the knee fully on their own, it will likely not lead to improved function outside of the brace (which may be possible with robotic or FES –augmented devices). After design improvements are addressed, we plan to evaluate the FreeGait in adults with crouch gait to assess safety, feasibility and initial effectiveness with the long-term goal of creating an affordable tool to reduce crouch and increase daily mobility.
REFERENCES
- [ ] T. A. Wren, S. Rethlefsen, and R. M. Kay, "Prevalence of specific gait abnormalities in children with cerebral palsy: influence of cerebral palsy subtype, age, and previous surgery," J Pediatr Orthop, vol. 25, pp. 79-83, Jan 2005
- E. Pröbsting, A. Kannenberg, and B. Zacharias, "Safety and walking ability of KAFO users with the C-Brace® Orthotronic Mobility System, a new microprocessor stance and swing control orthosis," Prosthetics and Orthotics International, vol. 41, no. 1, pp. 65-77, 2017.
- Wren TA, Dryden JW, Mueske NM, Dennis SW, Healy BS, Rethlefsen SA. Comparison of 2 orthotic approaches in children with cerebral palsy. Pediatr Phys Ther. 2015 Fall; 27(3):218-26. doi: 10.1097/PEP.0000000000000153.
- Z. F. Lerner, D. L. Damiano and T. C. Bulea, "The Effects of Exoskeleton Assisted Knee Extension on Lower-Extremity Gait Kinematics, Kinetics, and Muscle Activity in Children with Cerebral Palsy," Scientific Reports, vol. 7, (1), pp. 13512, 2017.
- J. Chen, D. Nichols, E. B. Brokaw, and P. S. Lum, "Home-Based Therapy After Stroke Using the Hand Spring Operated Movement Enhancer (HandSOME)," (in eng), IEEE Trans Neural Syst Rehabil Eng, vol. 25, no. 12, pp. 2305-2312, Dec 2017.
- Chen and P. S. Lum, "Pilot testing of the spring operated wearable enhancer for arm rehabilitation (SpringWear)," (in eng), J Neuroeng Rehabil, vol. 15, no. 1, p. 13, Mar 2 2018.
- J. Hidler, D. Brennan, I. Black, D. Nichols, K. Brady, and T. Nef, "ZeroG: overground gait and balance training system," (in eng), J Rehabil Res Dev, vol. 48, no. 4, pp. 287-98, 2011, doi: 10.1682/jrrd.2010.05.0098.