Abbey M. Fraser 1, Grant R. Bevill 1, Mary S. Lundy 1, Juan Aceros 1
1University of North Florida
INTRODUCTION
Toy-related injuries have increased substantially from 1990 to 2011 due to the increasing popularity and availability of battery-powered ride-on toys. According to the US Consumer Product Safety Commission, injuries associated with ride-on toys have increased in this time period by 73.7%. Furthermore, 77.6% of ride-on toy-related injuries were due to falls, passenger excursion, and impact with the interior of the vehicle[1]. In response, manufacturers have begun incorporating lap belts to the commercially available toys. These types of ride-on toys have gained great popularity as alternative mobility devices for children with disabilities and are widely used as early intervention tools. However, rehabilitation programs often modify these vehicles to incorporate 5-point harnesses to increase postural support for children with impaired mobility and poor trunk control.
The purpose of this study was to establish an experimental method for evaluating child safety in ride-on toy cars, to evaluate the effects of the addition of a lap belt, and to explore the effects of replacing the lap belt with a multipoint restraint system, such as a 5-point harness.
Limitations exist in the knowledge of pediatric safety testing and tolerance thresholds. Common safety testing methods include: volunteer test subjects, cadaver testing, the use of anthropomorphic test dummies (ATDs), and computer simulations. As children, especially those with disabilities, are unable to volunteer as test subjects, and child cadavers are not readily available, these are not viable options for analyzing pediatric safety. Furthermore, testing with live occupants involves additional complications, such as occupants anticipating and bracing for collision, and difficulties in calculating internal loads. ATDs are typically used to model the average child; however, the use of these is often expensive. Therefore, computer simulations represent the most viable alternative and were chosen for this study.
METHODS
The study consisted of simulating a powered ride-on toy car containing a 50th percentile six-year-old Hybrid III finite element (FE) model. This model represents the size and biomechanical properties of a typical six-year old. The simulation consisted of a frontal impact: 1) without a seatbelt, 2) with a lap belt, and 3) with a 5-point harness. The computer program LS-DYNA was chosen as the simulation tool because it is capable of highly non-linear, transient dynamic finite element analysis using explicit time integration.
Impulse
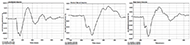
Crash testing was conducted using a commercially available ride-on toy car (12V-powered Mercedes AMG G63 ride-on battery powered car) to acquire experimental frontal impact data to supply as an acceleration impulse to the FE model. This was done using a live occupant of similar weight to that of the 6YO Hybrid III dummy (~50lbs). Three impact speeds were tested, as there were three speeds available on the remote control of the vehicle. The reported speed range is ~2.5-5 km/h per the vehicle manual. The low, medium, and high speeds were experimentally found to be 1.37 mph, 2.25 mph, and 3.05 mph, respectively. Prior testing was conducted to determine the distances at which the car reached steady state speed, and an additional five feet was added to ensure a constant velocity. For the low, medium and high speed impacts, the car impacted a wall from 10 feet, 15 feet, and 25 feet, respectively. A PCB Piezotronics, Inc. (SN 115452) accelerometer was placed in the center of the floorboard of the car and operated at 10,000 Hz per SAE standard J211-1 [2]. In addition, high-speed photography was used to capture each test. The vehicle was driven remotely into a wall at each of the three speeds, three times, for a total of nine tests. The data was filtered using MATLAB and cropped to only include the impulse and the vehicle's return to zero acceleration, exported to Microsoft Excel, and then imported directly into LS-DYNA. Only the forward movement impulse (y-direction) was used in the simulation since the x- and z-directions were negligible. For each speed, the most severe case was used in the FE simulations (Fig.1).
Occupant Modeling
The FE model, which replicated the interior of a ride-on toy car, was created using shell elements and rigid material properties (*MAT_RIGID). The sled was composed of two parts: the seat and the dashboard. It was constrained in all directions except the y-direction. The six-year-old Hybrid III model was then placed in an appropriate seated position in the vehicle environment. Automatic surface-to-surface contact was used to define contact between the seat and the axial skeleton, and between the feet and dashboard. Gravity was applied to the system for 150 milliseconds to allow the human model to settle into the seat, after which a load curve was applied using one of the three acceleration impulses from testing. The sled was constrained to a massless node, and a prescribed motion was applied using the massless node and the load curve.
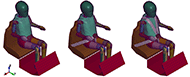
The lap belt and 5-point belt were created as a mixed belt (a belt containing both 1D seatbelt elements and 2D triangular, shell elements). The material of the 1D belts was defined using *MAT_SEATBELT and used loading and unloading curves. The material of the 2D shell component of the seatbelt was defined using *MAT_FABRIC with material values found experimentally for modeling seatbelts in LS-DYNA [3]. Contact between the dummy and the seatbelt was defined between the axial skeleton and the belt using automatic surface-to-surface contact. The three final models are shown below in Fig. 2.
The following injury metrics were calculated to quantify the results: head injury criterion (HIC), peak angular acceleration (PAA), peak linear acceleration (PLA), head and chest displacement, neck tension force, neck injury criterion (Nij), neck bending moment, and neck transverse shear.
RESULTS
Results indicate a uniform decrease in chest displacement with the addition of a lap belt, and further decreases with the addition of a 5-point harness [Table 1]. Head displacement subtly increased with the use of a lap belt, but decreased in all cases with a 5-point harness. From an absolute perspective, injury metrics were very low in all test conditions. In most cases, injury metrics tended to increase by modest amounts with the addition of either restraint condition. However, this trend was not uniformly present – several injury metrics decreased modestly and some increased markedly with the addition of restraints.
Speed | HIC15 | PAA (rad/ msec^2) | PLA (g's) | Head Displace- ment (mm) | Chest Displace- ment (mm) | Neck Force Tension (kN) | Nij | Neck bending moment (kN-mm) | Neck Transverse Shear (GPa) | |
---|---|---|---|---|---|---|---|---|---|---|
No Seatbelt | High | 0.192 | 0.036 | 5.546 | 179.0 | 159.6 | 0.113 | 0.038 | 0.448 | 0.287 |
Medium | 0.181 | 0.026 | 3.947 | 154.5 | 134.7 | 0.079 | 0.025 | 0.429 | 0.284 | |
Low | 0.176 | 0.017 | 4.387 | 94.9 | 105.9 | 0.037 | 0.014 | 0.471 | 0.287 | |
Lap Belt | High | 0.332 | 0.071 | 10.543 | 184.0 | 138.9 | 0.148 | 0.055 | 0.275 | 0.343 |
Medium | 0.174 | 0.062 | 2.492 | 157.4 | 122.7 | 0.109 | 0.037 | 0.465 | 0.284 | |
Low | 0.185 | 0.016 | 5.061 | 94.9 | 101.7 | 0.053 | 0.019 | 0.128 | 0.284 | |
5-point belt | High | 1.599 | 0.083 | 4.779 | 156.0 | 124.5 | 0.377 | 0.136 | 1.005 | 0.285 |
Medium | 0.213 | 0.048 | 4.253 | 137.7 | 115.6 | 0.109 | 0.037 | 0.465 | 0.284 | |
Low | 0.182 | 0.034 | 3.290 | 93.1 | 101.7 | 0.063 | 0.023 | 0.196 | 0.282 |
HIC15
HIC15 scores tended to increase with the addition of a seatbelt. For both the lap belt and 5-point harness models, the medium and low speed impulses resulted in minor increases of HIC15. The lap belt model at high speed moderately increased. However, the 5-point harness model with high-speed impulse resulted in a score more than three times greater than that of any other simulation, 1.599.
PAA and PLA
The greatest PLA experienced was 10.5g's with the lap belt model at high-speed. Every other model and speed experienced 5g's or less. PAA increased in nearly every instance with increasing occupant constraint.
Neck Bending Moment and Shear
Neck bending moment decreased at low speed for both the lap belt and 5-point belt, but experienced an increase at high-speed with the 5-pont belt. For medium speed the increase was negligible. Neck shear decreased minimally in almost all cases with the addition of seatbelts, with the high-speed lap belt being the only condition to increase.
DISCUSSION
Displacement
The 5-point harness was the best performer for decreasing chest and head displacement, most notably for medium and high-speed impacts. While the lap best functioned to reduce chest displacement, it was not effective at preventing forward displacement of the head.
Injury Metrics
Seatbelts provide a mechanism for earlier and more effective deceleration of the body – thereby preventing injurious contact with interior components – but may alter magnitudes of injury metrics from inertial loading as consequence. For example, the addition of a seatbelt restricts the chest and has been observed to cause an increase in head acceleration in the context of motor vehicle collisions [5]. However, despite any changes to injury metrics observed in our simulations, all values were very small in comparison to known injury tolerance thresholds.
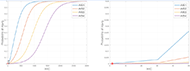
For example, while the peak head accelerations increased due to additional contact with the seatbelt, studies have concluded that peak linear accelerations on the order of ten g's can be experienced in activities of daily living [4] . No PLA values exceed ten g's except the lap belt with high-speed impulse which minimally exceeds this value. All recorded HIC values were extremely small when compared to AIS injury thresholds (Fig. 3) [6]. The maximum HIC score recorded, 1.599, corresponds to a probability of an AIS1 injury of 2.7 x 10-39. This HIC score likely increased due to the high-speed impact and additional contact with the seatbelt.
CONCLUSION
Results indicate that occupant displacement can be reduced by the use of a lap belt, and further reductions in displacement are achieved with a 5-point harness. As the greatest concerns for these ride-on toys are related to displacement (e.g., falls or impact with the interior of the vehicle), findings from this study support the use of these types of restraint systems. In most cases, injury metrics tended to increase by modest amounts with the addition of either restraint condition, however, this trend was not uniformly present – several injury metrics decreased modestly and some increased markedly with the addition of restraints. Instances where injury metrics increased substantially occurred in high-speed impact conditions, where PLA from the lap belt test and HIC15 from the 5-point harness test increased substantially relative to the unbelted condition. Within this context, an avenue of future research could involve the development of a restraint system for ride-on toys that exhibits more uniform behavior across impact speeds. Regardless, none of the collected injury metrics ever approach known tolerance thresholds [5], and most injury metrics are well within the range that a child experiences in daily life [4] Taken together, these results support the use of a 5-point harness system to minimize displacement-related injury mechanisms with little-to-no added risk in inertial injury metrics. This study provides a reliable framework to simulate ride-on toy collision events, which can be used in future studies to evaluate the safety of the toys as they are applied in a rehabilitation setting, such as with children with disabilities
REFERENCES
- C. Gaw et al, "Toy-Related Injuries Among Children Treated in US Emergency Departments, 1990-2011," Clin. Pediatr., vol. 54, (2), pp. 127-137, 2015. Available: https://login.dax.lib.unf.edu/login?url=http://search.ebscohost.com/login.aspx?direct=true&db=edswsc&AN=000348197200004&site=eds-live&scope=site.
- Anonymous "(R) Instrumentation for Impact Test - Part 1 - Electronic Instrumentation," Mar, 2014.
- S. Kang et al, "LS-DYNA® Belted Occupant Model," Https://Www.Dynalook.Com/Conferences/15th-International-Ls-Dyna-Conference/Occupant-Protection/Ls-Dyna-R-Belted-Occupant-Model, 2018.
- W. Bussone, "Linear and Angular Head Accelerations in Daily Life." , Virginia Tech, 2005.
- A. K. Abbas, A. F. Hefny and F. M. Abu-Zidan, "Seatbelts and road traffic collision injuries," World Journal of Emergency Surgery : WJES, vol. 6, (1), pp. 18, 2011. Available: https://www.ncbi.nlm.nih.gov/pubmed/21619677. DOI: 10.1186/1749-7922-6-18.
- W. C. Hayes, M. S. Erickson and E. D. Power, "Forensic Injury Biomechanics," Annual Review of Biomedical Engineering, vol. 9, (1), pp. 55-86, 2007. Available: https://www.ncbi.nlm.nih.gov/pubmed/17447861. DOI: 10.1146/annurev.bioeng.9.060906.151946.