Danielle Vaithilingam1
, Ivan Vuong
1
, Robert Huang
1
, Jackelyn Navar
1
, Yurie Hong
1
, Nyeli Kratz
1
, Rachel Li
1
, Ashley Koenig
1
, Stacy Suskauer
2
, Christopher Joseph
2
, Shababa Matin
1
1 Johns Hopkins University, Department of Biomedical Engineering, 2
Kennedy Krieger Institute
Problem Statement and Background
Over 4,000 pediatric patients in the United States have cerebral palsy (CP) or a traumatic brain injury that leads to hemiplegia, the weakness or paralysis of muscle in one side of the body [1]. Because these children struggle with motor control in one or both legs and one of their arms, they are confined to wheelchairs and therefore experience severe physical and mental health consequences.
Walking ability in patients with CP is characterized using the five-category Gross Motor Function Classification System (GMFCS). Of interest to this team are patients with a GMFCS level of IV, who are unable to walk on their own, even with the aid of handheld mobility devices like walkers, but can stand upright with sufficient support [2]. Although patients maintain full motor function in their unaffected limbs, those with severe hemiplegia (corresponding to GMFCS level IV) rely upon wheelchairs for mobility [2]. As a result, these patients may suffer from a lack of independence, which contributes to feelings of depression, anxiety, and social inequality, as well as severe physiological consequences due to extensive wheelchair use. The health consequences of prolonged sitting include respiratory, circulatory, muscular, and gastrointestinal issues that may lead to tens of thousands of dollars in medical costs per patient [3]. Although these issues can be alleviated with a few hours of daily standing, static standing devices do not provide the independence and physical exercise that manual self-propulsion devices do.
Pediatric patients with hemiplegia and a GMFCS level of IV would benefit greatly from an assistive standing mobility device driven with their functioning arm. Standing mobility promotes recovery during the rehabilitation process and avoids the complications of prolonged sitting by improving respiration, muscle health, bone density, and bowel function [4]. It also strengthens both the leg and trunk muscles and the neural connections that control those muscles, increasing the user's recovery potential [5]. Manual self-propulsion provides the additional respiratory and cardiovascular health benefits of physical exercise, which patients who rely on motorized wheelchairs may lack [4]. In addition to physiological benefits, standing mobility also increases a patient's ability to perform instrumental activities of daily living, a metric of independence, and promotes social development by allowing the user to participate in standing activities with peers [6]. Standing is also associated with greater mental alertness and improved academic performance, which contribute to a patient's quality of life [7].
While assistive standing mobility devices can alleviate the consequences of prolonged sitting, current options are not feasible for this patient population. Because individuals in the target population have only one fully functioning arm, they cannot efficiently use existing mechanical standers, which require two-arm propulsion. A basic motorized stander, which allows the patient to control their motion with a joystick, however, costs upwards of $10,000 and is often not covered by insurance, making it unaffordable for many patients [8]. Motorized standers also fail to offer the additional cardiovascular and respiratory benefits of manual propulsion. Pediatric patients with a GMFCS level of IV and one impaired arm need an affordable means of independent standing mobility in order to improve their physical and social health and development.
Methods/Approach
To develop design requirements for the novel mobile stander, the team reviewed two-arm-drive, mechanical mobile standers and one-arm-drive (OAD) mechanisms used in wheelchairs. The team solicited feedback from patients and physical therapists through in-person interviews to identify problems with existing technologies as well as necessary stander features.
Because stakeholder feedback revealed few issues with current mobile stander frames, the novel stander's frame was designed to be structurally comparable, with some modifications to accommodate the OAD propulsion mechanism. The team identified multiple issues with existing OAD mechanisms, including potential pinched fingers, a lack of intuitivity, and incompatibility with standers. To combat these issues, a single rim propulsion mechanism was designed, utilizing a gearbox for directional control. From evaluation of patient experiences with traditional mobile standers and OAD mechanisms and accounting for additional requirements relating to the existence of misalignment in the gearbox, the following design requirements were generated. The OAD mobile stander must:
- Safely maintain patients in an upright position. The stander must have a tilting angle and tilting force greater than or equal to 42o and 88 N, respectively, to meet or exceed the stability of competitors.
- Function with one-hand propulsion. To allow for use by children ages 6+, the stander must have a maximum starting push force of 30 N on carpet. When the stander is in motion at 0.43 m/s (median velocity), it must have a maximum stopping force of 34.5 N and a maximum stopping distance of 10 cm to ensure safe stopping without collisions.
- Be able to travel in ADA-compliant hallways. The stander must not exceed 32" width and 60" turning diameter to be able to maneuver in ADA-compliant hallways [9].
- Be able to move and turn with minimal drifting. When shifting from rotational to linear movement, the re-engagement of the propulsion mechanism must not cause the base of the stander to turn more than 2.86° in either direction. This will allow users to travel within a 2" margin of their intended direction for 40 feet, for example in an ADA-compliant hallway.
- Be cost effective. To be cost effective, the stander price should not exceed $7000, which is less than two-thirds the price of a motorized stander and no more than one third greater than the price of a two-arm-drive stander.
Final Approach and Design
To develop an OAD mobile stander, the team first considered its two components: stander frame and propulsion mechanism.
A frame was designed based on existing standers, with modifications made to integrate the novel propulsion mechanism (Fig. 1(a)). The frame design features adjustable knee, hip, and chest supports that keep the user in an upright position. The footplate was placed low to the ground to position children close to their developmental height group, promoting social interaction. The base of the frame was made wide enough to be stable while fitting in ADA-compliant hallways. Arches on each side of the frame support the axles and provide a base for the lever system (Fig. 1(b)).
Existing OAD mechanisms in wheelchairs have two main issues that make them incompatible with the new stander. First, double-rim systems lack intuitivity. Patients often have difficulty maneuvering when steering controls for both wheels are on one side of their torso because they must recall which direction to rotate each hand rim to move left versus right. Other OAD mechanisms, like lever drives, require inputs that cannot be provided by a stander user, like leg-based steering. In a stander, the use of the legs for steering is not viable as the user is secured by the supports to prevent injury.
The team designed an original OAD mechanism to avoid the issues of existing mechanisms. A single drive rim was selected because it provides the user with the most fluid control over the direction and speed of wheel rotation. Stakeholder feedback indicated that this system also avoids issues like pinching and low intuitivity associated with double rim drive systems. The team interviewed stakeholders to determine whether a steering mechanism that swivels the stander in place (by turning the drive wheels at the same speed in opposite directions) or one that gradually turns (by turning the caster wheels) was necessary. The team focused on swiveling, which is more suitable for tight spaces like kitchens where the stander will be used.
To allow for swiveling, the team designed a gearbox that transfers the rotational motion of the drive wheel to the non-drive wheel at the same magnitude (Fig. 1(c)). The direction of the non-drive wheel's rotation is controlled by a lever. In the forward lever position, which is referred to as "straight mode", the wheels turn in the same direction, causing the stander to move in a straight line. In the back lever position, or "swivel mode", the wheels turn in opposite directions, causing the stander to rotate about its vertical axis.
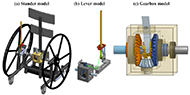
The benefits of this propulsion mechanism are increased ease of propulsion and decreased risk of pinching compared to a double-rim system. The drawbacks are the need to stop before shifting between straight and swivel mode and the existence of misalignment between the clutch and gears, which causes the stander to rotationally drift during shifting.
Testing Outcomes
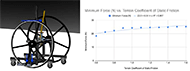
Testing was conducted in SolidWorks on the assemblies in Fig. 1. Static analysis of the stander while applying a 2000 N downward load on the footplate area indicated that the stander frame can withstand 200 kg, or about 441 lbs, which is greater than the weight of most individuals in the pediatric population.
Motion studies revealed that 156 N of horizontal force against the top of the handrim and toward the center of the stander was the minimum required to tilt the stander about the opposite wheel to its 56° angle of instability, at which point the center of mass was directly above the opposite wheel's point of contact with the ground.
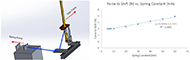
From the motion study on a virtual carpet with a static coefficient of friction of 1.6, the minimum force that a user must apply at the handrim to propel the stander is 25.23 N [10]. This force can be output by users 6 years of age and older in a standing position (Fig. 2) [11,12]. The coefficients of friction, and thus the necessary propulsion force, of other indoor flooring options are lower and thus usable with the stander.
Motion studies indicated that the force required to shift the lever position remained below 5 N when using a spring in the shifter mechanism with a spring constant up to 60 N/m (Fig. 3).
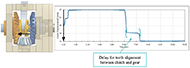
The maximum unintentional rotation of the stander base due to clutch misalignment was found to be 71.6° based on the maximum 1.18-second duration, 36" diameter of the drive wheels, and 32" diameter of the stander base (Fig. 4).
Our goal was to create a mechanical, OAD mobile stander to give pediatric patients with hemiplegia the benefits of standing mobility, including improved muscle tone, improved cardiovascular and respiratory health, and increased independence and social health. To achieve this goal, the stander needed to safely support patients in an upright position, function reliably with one-hand propulsion, and be able to move and turn with minimal drifting.
Through simulations in SolidWorks, the team determined that the described stander design meets the first two requirements but not the third. The unintentional stander rotation while shifting was over 70o, exceeding the < 3o requirement. The gearbox mechanism thus needs to be adjusted or completely redesigned. After these changes are made, the team will complete a physical prototype that can be utilized for intuitivity and usability testing with human subjects.
Cost and Pricing
Due to the COVID-19 emergency situation, the physical prototype of our stander could not be completed. We estimate the total production cost of the stander to be about $2,400 from the cost of materials purchased and manufactured for the prototype. This includes $1,400 for the frame and gearbox components and $1,000 for the standard drive wheels, which would be included in the commercial version. This total cost would likely decrease when produced in large quantities. Our OAD mobile stander would be priced around $5,500. This price point is comparable to the cost of similar products such as the Rifton mobile stander, but still significantly reduces the cost burden for the patient when compared to motorized standers.
Significance
Children with hemiplegia are vulnerable to the negative physical and psychological consequences of limited mobility and prolonged wheelchair use. An affordable means of independent standing mobility, which would mitigate these effects as well as improve independence, currently does not exist for this underserved patient population. Our novel OAD mobile stander design has the potential to help these individuals engage with their environment, build their sense of independence, and improve their quality of life.
Future Directions
In order to ensure that our stander meets all of our design goals, the team will be improving the design of the propulsion mechanism to eliminate gear slop and unintentional drifting. In addition, the team has prepared a survey to collect feedback on the intuitivity of the lever-based swivel steering method as well as the necessity of adding a gradual turning mechanism in addition to the swivel mechanism. If the addition of a gradual turning mechanism is deemed necessary, it will be incorporated during the redesign.
After the redesign is complete, the new design will be incorporated into the existing prototype frame and, upon the completion of the prototype, the team will conduct an intuitivity and usability test of the stander.
References
- CDC. (2019, April 30). What is Cerebral Palsy? | CDC. Retrieved from https://www.cdc.gov/ncbddd/cp/facts.html.
- Palisano, R., Rosenbaum, P., Bartlett, D., Livingston, M. (2007). Gross Motor Function Classification System. Retrieved from https://www.canchild.ca/system/tenon/assets/ attachments/000/000/058/original/GMFCSER_English.pdf
- Vega, J. (2019, September 7). Hemiplegia and Hemiparalysis. Retrieved from https://www.verywellhealth.com/information-about-hemiplegia-3146139.
- Goodman R. Psychological aspects of hemiplegia. Archives of Disease in Childhood [Online] 1997;76(3):177-178. Available from: doi:10.1136/adc.76.3.177
- Joseph, C. (2019, October 9). Personal interview.
- Else Odding, Marij E. Roebroeck & Hendrik J. Stam. (2006). The epidemiology of cerebral palsy: Incidence, impairments and risk factors. Disability and Rehabilitation, 28(4), 183-191. doi: 10.1080/09638280500158422
- Paleg, Smith & Glickman. Paleg GS, Smith BA, Glickman LB. Systematic review and evidence-based clinical recommendations for dosing of pediatric supported standing programs. Pediatric Physical Therapy : The Official Publication of the Section on Pediatrics of the American Physical Therapy Association [Online] 2013;25(3):232–247. doi: 10.1097/pep.0b013e318299d5e7
- American Quality Health Products. Karman XO-505 Power Standing Wheelchair. [Online]. Available from: https://americanqualityhealthproducts.com/all-power-chairs/3944-xo-505 -standing-wheelchair-w-multiple-power-functions-by-karman.html#/
- ADA Standards for Accessible Design. (2010). Retrieved October 30th, 2019, from https://www.ada.gov/2010ADAstandards_index.htm
- Li, K. W., Chang, W.-R., Leamon, T. B., & Chen, C. J. (2004). Floor slipperiness measurement: friction coefficient, roughness of floors, and subjective perception under spillage conditions. Safety Science, 42(6), 547–565. doi: 10.1016/j.ssci.2003.08.006
- CCOHS. (2020). Pushing & Pulling - General. Retrieved from https://www.ccohs.ca/oshanswers/ergonomics/push1.html
- Disabled World. (2017). Average height to weight chart: babies to teenagers. Retrieved from https://www.disabled-world.com/calculators-charts/height-weight-teens.php
- Sonenblum, S.E., Sprigle, S.H., & López, R.A. (2012). Manual Wheelchair Use: Bouts of Mobility in Everyday Life. Rehabilitation Research and Practice, 2012.
Acknowledgments
We thank our faculty advisors Mr. Tom Benassi, Staff Engineer, Department of Biomedical Engineering, JHU; Ms. Bailey Surtees, Teaching Assistant, Department of Biomedical Engineering, JHU; and our committee member Dr. Scott Paul, Senior Staff Physiatrist, NIH, Assistant BME Professor, JHU for their continued support in the execution of our project and research.